Operating Principle of a Boiler
I./Operating Principle of a Boiler and Safety Measures
Operating Principle of a Boiler
A boiler, also known as a steam generator, is a device that converts water into steam using heat generated from fuel combustion. This steam is then used for various industrial purposes such as heating, power generation, and running machinery. Below is a basic overview of how a boiler operates:
-
Fuel and Combustion System:
-
Fuel: Fuel, which can be coal, oil, gas, or biomass, is fed into the boiler's combustion chamber.
-
Combustion: The fuel is burned in the combustion chamber, generating heat. This process requires a supply of air or oxygen to sustain combustion.
-
-
Heat Transfer:
-
Direct Heat Transfer: The heat generated from combustion is directly transferred to water through the heat exchange surfaces of water tubes or steam pipes.
-
Convection and Radiation Heat Transfer: Heat is also transferred via radiation from the flame and convection from the combustion gases.
-
-
Water to Steam Conversion:
-
Water Reservoir: Water is stored in a reservoir and comes into contact with the heat exchange surfaces.
-
Boiling and Evaporation: As heat is transferred to the water, its temperature rises until it reaches the boiling point and begins to evaporate, producing high-pressure steam.
-
-
Steam Collection and Utilization:
-
Steam Collection: The generated steam is collected and directed through steam pipes to various systems for utilization.
-
Steam Use: The steam is used to generate mechanical power, heat, or electricity.
-
II/ Safety Measures for Boilers
Ensuring safety in boiler operation is crucial. Here are several safety measures to protect boiler operations:
-
Pressure Control Systems:
-
Safety Valves: Safety valves are installed to release excess pressure if it exceeds safe levels.
-
Pressure Gauges: These help monitor and ensure pressure remains within safe limits.
-
-
Temperature Control Systems:
-
Temperature Sensors: These monitor the water and steam temperature to ensure it does not exceed safe levels.
-
Thermostats: Automatically adjust the temperature to maintain safe operating conditions.
-
-
Water Level Control:
-
Water Level Alarms: Warn when the water level is too low or too high, preventing damage from water shortage or overflow.
-
Feed Water Controllers: Ensure a continuous and stable supply of water to the boiler.
-
-
Emergency Protection Systems:
-
Emergency Shut-off Systems: Allow immediate shutdown of the boiler in case of emergency.
-
Safety Switches: Automatically cut off power if any faults or hazards are detected.
-
-
Regular Maintenance and Inspection:
-
Routine Maintenance: Regularly inspect and maintain the boiler to ensure all components function properly.
-
Comprehensive Inspections: Perform detailed inspections, including pressure testing, water quality testing, and safety device checks.
-
-
Training and Education of Personnel:
-
Safety Training: Ensure operators are thoroughly trained in safety procedures and boiler operation.
-
Ongoing Training: Provide regular updates and training sessions to keep personnel informed about the latest safety practices and technologies.
-
By implementing these measures, boiler operation becomes safer, reducing the risk of accidents and ensuring efficient production while protecting the health and safety of workers.
Related News
Overview Introduction to the Industrial Valve Industry in Vietnam and its Challenges
31/05/2024
Introduction to Industrial Valve Industry in Vietnam: The industrial valve industry in Vietnam is an important and indispensable part of the national industrial infrastructure. Industrial valves play a key role in controlling the flow of liquids, gases, and vapors in industrial systems. Common valve types include ball valves, gate valves, butterfly valves, pressure reducing valves, pressure regulator valves, and safety valves. These valves are widely used in many fields such as oil and gas, chemicals, water supply and drainage, food and beverage, pharmaceuticals, and energy.
Operation Process of an Air Compressor
01/06/2024
Air compressors are crucial devices in many industries, providing compressed air for various tools and equipment. Understanding the operation process of an air compressor helps ensure the efficiency and longevity of the system. Below is a detailed description of the operation process of a typical air compressor, including its main components and operational steps. 1. Basic Components of an Air Compressor
Operation Process of a Pump
01/06/2024
Pumps are vital components in numerous industrial systems, used for moving fluids such as water, chemicals, oil, and other liquids. Understanding how a pump operates is essential for ensuring efficient and reliable performance. Below is a detailed description of the operation process of a typical industrial pump, including its main components and steps involved in its operation.
Operation Process of a Heat Exchanger
01/06/2024
A heat exchanger is an essential component in many industrial systems, facilitating the transfer of heat between two or more fluids without them coming into direct contact. Below is a detailed explanation of the operation process of a heat exchanger, including its main components and operational steps.
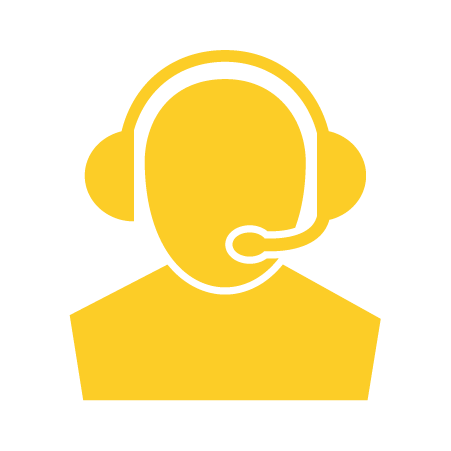
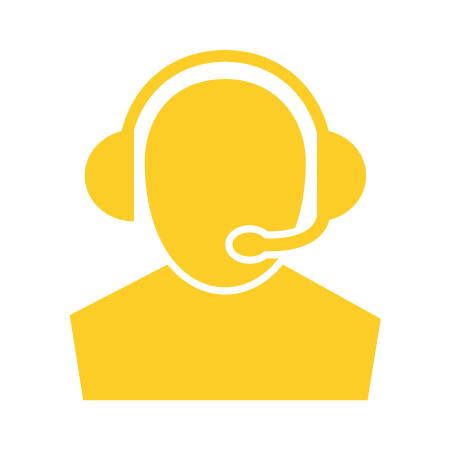
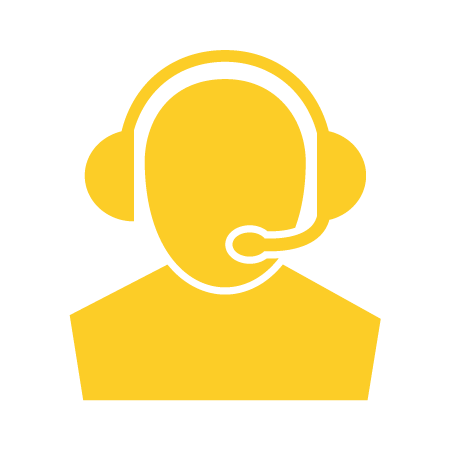
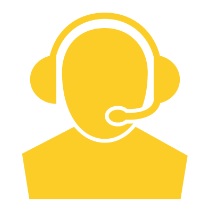
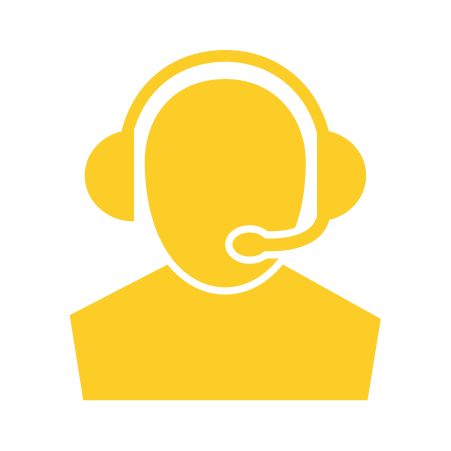