Operation Process of a Heat Exchanger
Operation Process of a Heat Exchanger
A heat exchanger is an essential component in many industrial systems, facilitating the transfer of heat between two or more fluids without them coming into direct contact. Below is a detailed explanation of the operation process of a heat exchanger, including its main components and operational steps.
1. Basic Structure of a Heat Exchanger
Main Components:
- Tubes: The hot or cold fluid flows through these tubes.
- Shell: Encases the tubes and the other fluid flows around the tubes within the shell.
- Baffles: Direct the flow of the fluid inside the shell, increasing heat exchange efficiency.
- Inlet and Outlet: Points where the fluids enter and exit the heat exchanger.
2. Operating Principle of a Heat Exchanger
Operation Process:
-
Preparing the Fluids:
- Hot Fluid: Is pumped into the heat exchanger through the inlet. This fluid has a higher temperature and needs to be cooled.
- Cold Fluid: Is pumped into the heat exchanger through another inlet. This fluid has a lower temperature and will absorb heat from the hot fluid.
-
Fluid Circulation:
- Hot Fluid: Flows through the tubes inside the heat exchanger.
- Cold Fluid: Flows around the tubes within the shell.
-
Heat Exchange:
- Heat Transfer Through Tube Walls: Heat from the hot fluid transfers through the tube walls to the cold fluid. Since the fluids do not directly contact each other, heat is transferred through the walls by conduction.
- Baffles: Inside the shell direct the flow of the cold fluid, ensuring it flows over the entire heat exchange surface, increasing heat transfer efficiency.
-
Fluid Exit:
- Cooled Hot Fluid: Exits the heat exchanger through its outlet.
- Heated Cold Fluid: Exits the heat exchanger through its outlet.
-
Temperature Control:
- Automated control systems can be used to adjust the flow rates and temperatures of both fluids, ensuring optimal performance of the heat exchanger.
3. Types of Heat Exchangers
Shell and Tube Heat Exchanger:
- Structure: Consists of a bundle of tubes (tube bundle) inside a shell.
- Applications: Common in the oil, gas, chemical, and energy industries.
Plate Heat Exchanger:
- Structure: Consists of many thin metal plates stacked together with spaces for fluids to flow through.
- Applications: Often used in the food and beverage industry, HVAC systems.
Air Heat Exchanger:
- Structure: Uses fans to circulate air over a set of tubes or plates.
- Applications: Heating, ventilation, and air conditioning (HVAC) systems.
4. Advantages and Disadvantages of Heat Exchangers
Advantages:
- High Efficiency: Optimizes the heat exchange process between fluids.
- Energy Saving: Minimizes the amount of energy required for heating or cooling.
- Flexible Design: Available in various shapes and sizes to suit many applications.
Disadvantages:
- High Initial Cost: Heat exchangers can have a high upfront investment cost.
- Complex Maintenance: Requires regular inspection and maintenance to ensure efficiency.
- Risk of Blockage: Fluids containing particulates or impurities can cause blockages, reducing heat exchange efficiency.
5. Applications of Heat Exchangers
Oil and Gas Industry:
- Used to cool oils and chemicals during processing.
Food and Beverage Industry:
- Used to heat and cool food and beverage products.
Energy Industry:
- Used in power plants to recover heat from power generation processes.
HVAC Systems:
- Used in heating, ventilation, and air conditioning systems to regulate air temperature in buildings and industrial facilities.
Conclusion
Heat exchangers play a crucial role in many industries by optimizing the heat transfer process and saving energy. Understanding the operation process and applications of this equipment helps businesses enhance efficiency and ensure continuous operation of production systems.
Related News
Overview Introduction to the Industrial Valve Industry in Vietnam and its Challenges
31/05/2024
Introduction to Industrial Valve Industry in Vietnam: The industrial valve industry in Vietnam is an important and indispensable part of the national industrial infrastructure. Industrial valves play a key role in controlling the flow of liquids, gases, and vapors in industrial systems. Common valve types include ball valves, gate valves, butterfly valves, pressure reducing valves, pressure regulator valves, and safety valves. These valves are widely used in many fields such as oil and gas, chemicals, water supply and drainage, food and beverage, pharmaceuticals, and energy.
Operation Process of an Air Compressor
01/06/2024
Air compressors are crucial devices in many industries, providing compressed air for various tools and equipment. Understanding the operation process of an air compressor helps ensure the efficiency and longevity of the system. Below is a detailed description of the operation process of a typical air compressor, including its main components and operational steps. 1. Basic Components of an Air Compressor
Operation Process of a Pump
01/06/2024
Pumps are vital components in numerous industrial systems, used for moving fluids such as water, chemicals, oil, and other liquids. Understanding how a pump operates is essential for ensuring efficient and reliable performance. Below is a detailed description of the operation process of a typical industrial pump, including its main components and steps involved in its operation.
10 Most Important Industrial Equipment in Factories
01/06/2024
Modern industrial factories rely on a range of equipment to maintain high performance and ensure continuous operation. Below is a detailed description of the 10 most important types of industrial equipment, including their functions, applications, advantages, and disadvantages.
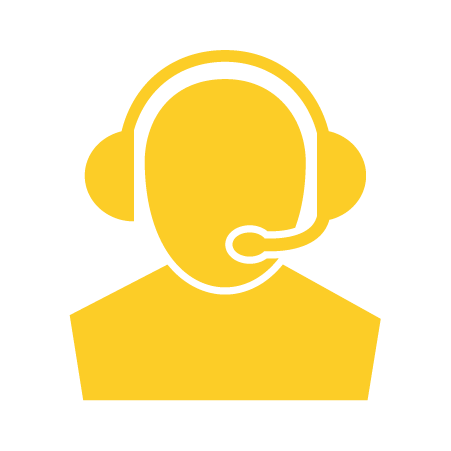
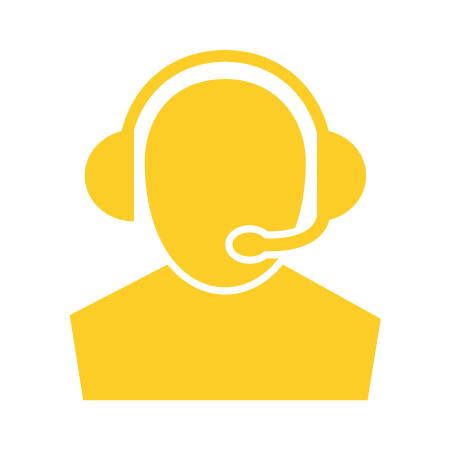
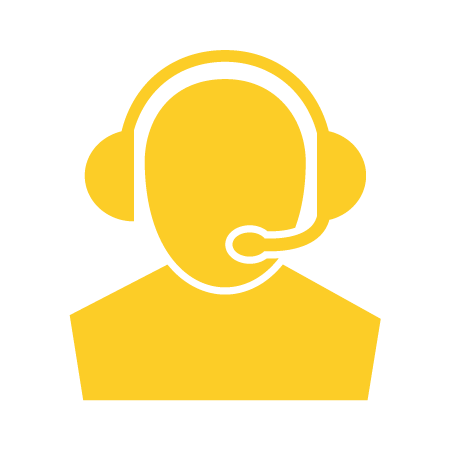
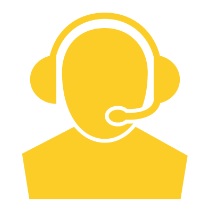
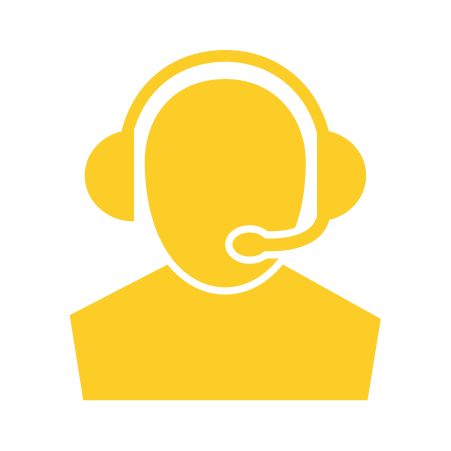