Operation Process of a Pump
Operation Process of a Pump
Pumps are vital components in numerous industrial systems, used for moving fluids such as water, chemicals, oil, and other liquids. Understanding how a pump operates is essential for ensuring efficient and reliable performance. Below is a detailed description of the operation process of a typical industrial pump, including its main components and steps involved in its operation.
1. Basic Components of a Pump
Main Components:
- Pump Housing (Casing): The outer shell that contains all internal components and directs the flow of the fluid.
- Impeller: A rotating part that transfers energy to the fluid.
- Shaft: Connects the impeller to the motor and transmits the rotational energy.
- Motor: Provides the power to rotate the impeller.
- Suction Inlet: The point where the fluid enters the pump.
- Discharge Outlet: The point where the fluid exits the pump.
- Seals and Bearings: Prevent leaks and support the rotating shaft.
2. Operating Principle of a Pump
Operation Process:
-
Fluid Entry (Suction):
- Initial State: The pump is filled with the fluid to prime it, ensuring there is no air inside.
- Suction Inlet: Fluid enters the pump through the suction inlet, driven by atmospheric pressure or another driving force.
-
Impeller Rotation:
- Motor Activation: The motor powers the pump, causing the shaft and impeller to rotate.
- Centrifugal Force: In centrifugal pumps, the rotating impeller creates centrifugal force, pushing the fluid outward from the center of the impeller to the edges.
-
Energy Transfer:
- Kinetic Energy: As the impeller rotates, it imparts kinetic energy to the fluid, increasing its velocity.
- Pressure Increase: The high-velocity fluid is directed to the pump casing, where its kinetic energy is converted into pressure energy.
-
Fluid Movement (Discharge):
- Flow Direction: The casing directs the pressurized fluid towards the discharge outlet.
- Fluid Exit: The fluid exits the pump through the discharge outlet, moving towards its intended destination within the system.
-
Continuous Operation:
- Cycle Repetition: The process of fluid entry, energy transfer, and discharge continues as long as the pump is in operation.
- System Control: Flow rate and pressure can be regulated using control valves and speed adjustments of the motor.
3. Types of Pumps and Their Operation
Centrifugal Pump:
- Operation: Uses an impeller to create centrifugal force to move the fluid.
- Applications: Water supply, irrigation, chemical processing.
Positive Displacement Pump:
- Operation: Traps a fixed amount of fluid and forces it through the discharge pipe.
- Applications: Hydraulic systems, oil and gas transfer, food processing.
Diaphragm Pump:
- Operation: Uses a diaphragm to create a vacuum that draws fluid into the chamber, then pushes it out.
- Applications: Chemical handling, slurry pumping, pharmaceuticals.
Gear Pump:
- Operation: Uses meshing gears to pump fluid by displacement.
- Applications: Lubrication systems, chemical mixing, fuel transfer.
4. Advantages and Disadvantages of Pumps
Advantages:
- Versatility: Suitable for a wide range of fluids and applications.
- Efficiency: High efficiency in transferring energy to the fluid.
- Reliability: Durable and capable of operating under various conditions.
Disadvantages:
- Initial Cost: High initial investment for high-quality pumps.
- Maintenance: Requires regular maintenance to prevent wear and tear.
- Energy Consumption: Can consume significant energy, especially in large systems.
5. Applications of Pumps
Water Supply and Irrigation:
- Pumping water for domestic and agricultural use.
Chemical Processing:
- Handling and transferring chemicals in industrial processes.
Oil and Gas Industry:
- Transferring crude oil, natural gas, and refined products.
Food and Beverage Industry:
- Pumping liquids and semi-liquids in food production.
HVAC Systems:
- Circulating water and other fluids in heating, ventilation, and air conditioning systems.
Conclusion
Understanding the operation process of a pump is crucial for maintaining its efficiency and reliability in various industrial applications. By comprehensively grasping how pumps work, operators can ensure optimal performance, reduce downtime, and extend the lifespan of these essential components in industrial systems.
Related News
Overview Introduction to the Industrial Valve Industry in Vietnam and its Challenges
31/05/2024
Introduction to Industrial Valve Industry in Vietnam: The industrial valve industry in Vietnam is an important and indispensable part of the national industrial infrastructure. Industrial valves play a key role in controlling the flow of liquids, gases, and vapors in industrial systems. Common valve types include ball valves, gate valves, butterfly valves, pressure reducing valves, pressure regulator valves, and safety valves. These valves are widely used in many fields such as oil and gas, chemicals, water supply and drainage, food and beverage, pharmaceuticals, and energy.
Operation Process of an Air Compressor
01/06/2024
Air compressors are crucial devices in many industries, providing compressed air for various tools and equipment. Understanding the operation process of an air compressor helps ensure the efficiency and longevity of the system. Below is a detailed description of the operation process of a typical air compressor, including its main components and operational steps. 1. Basic Components of an Air Compressor
Operation Process of a Heat Exchanger
01/06/2024
A heat exchanger is an essential component in many industrial systems, facilitating the transfer of heat between two or more fluids without them coming into direct contact. Below is a detailed explanation of the operation process of a heat exchanger, including its main components and operational steps.
10 Most Important Industrial Equipment in Factories
01/06/2024
Modern industrial factories rely on a range of equipment to maintain high performance and ensure continuous operation. Below is a detailed description of the 10 most important types of industrial equipment, including their functions, applications, advantages, and disadvantages.
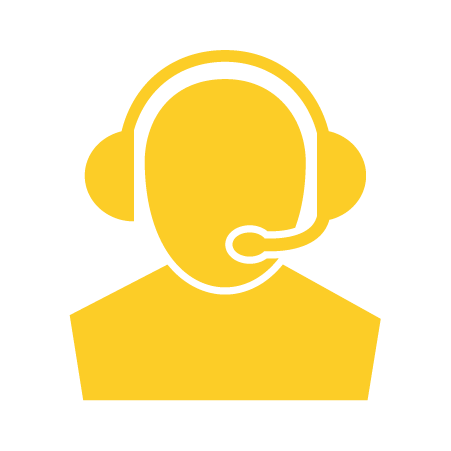
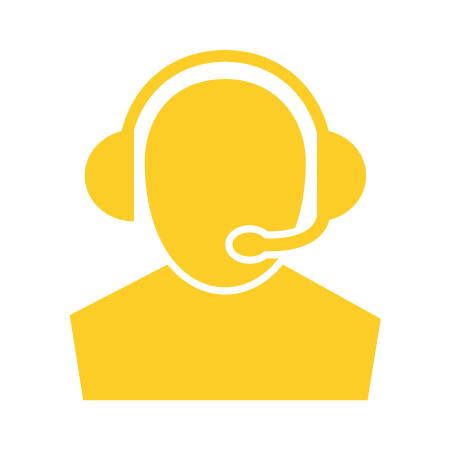
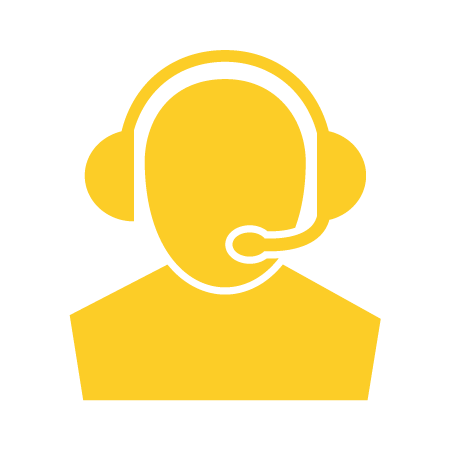
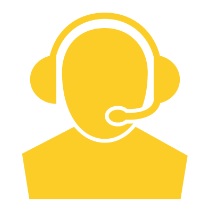
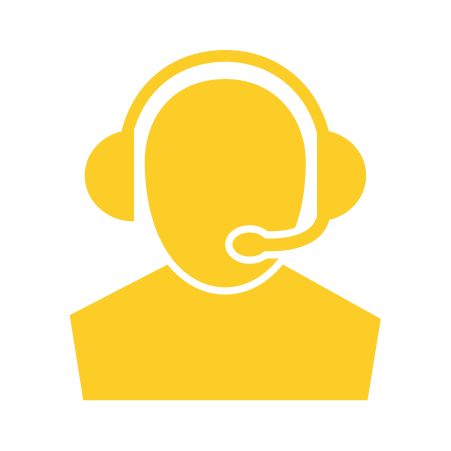