Steam trap
Price: Contact
ThermoDyne® Trap TLV A3N/AF3N
ThermoDyne® Trap
A3N/AF3N
Long life, best quality
The most versatile thermodynamic steam trap
Durability
- TLV products are designed from the outset to help minimize life cycle cost. The A3N is quality-made for durability, ensuring long-term stable operation.
Versatility
- With its high discharge capacity and pressure range up to 1.6 MPaG, the A3N can be used on a wide range of applications ‒ from steam mains to light processes.
Reliability
- The predecessor of the A3N, the A3, appeared in 1958. Ten times more durable than conventional traps in its day, this line is a longtime bestseller.
ThermoDyne Steam Trap Pamphlet (1571 KB)
Benefits and Features
Energy Conservation
- Steam loss due to adverse weather conditions such as rain and wind is drastically reduced by the steam jacketed pressure chamber.
Improved Productivity (Bimetal Type Automatic Air Venting Feature)
- Automatic air venting reduces start-up time, greatly improving productivity. Additionally, reductions in steam loss, fuel consumption and labor can be achieved by eliminating the need for manual blowdown at start-up.
Easy Maintenance
- The valve disc and valve seat can easily be replaced by removing the outer and inner covers. Traps can be repaired in-line without the need for specialized equipment.
Application Areas
-
Applications that do not require precise temperature control.
Steam Header | Steam Main (Drip) | Light Processes |
---|---|---|
![]() |
![]() |
![]() |
Product Details
Model | Photo | Connection | Body Material | PMO (MPaG) | Minimum Operating Pressure (MPaG) | TMO (°C) | Discharge Capacity (kg/h) | Specification |
---|---|---|---|---|---|---|---|---|
A3N |
|
Screwed | Ductile Cast Iron (FCD450) |
1.6 | 0.03 | 220 | 1700 | Specification |
Cast Iron(FC250) | ||||||||
AF3N | Flanged | Cast Iron (FC250) |
- PMO = Maximum Operating Pressure
- TMO = Maximum Operating Temperature
OVERVIEW
Steam-insulated jacket protects against adverse atmospheric conditions
In traps with a single-layer cap, adverse atmospheric conditions and radiant heat loss result in steam loss from no-load actuation and blowing. While this problem is partly solved with an air-insulated jacket, the A3N’s steam-heated and condensate-cooled jacket offers the greatest protection, ensuring the most stable operation of all thermodynamic steam traps.
Comparing the effect of external conditions by cap insulation
ThermoDyne® Disc Trap: Steam-Insulated Jacket
The ThermoDyne® disc type trap uses the steam jacketed pressure chamber to retain heat by steam and cool by condensate.
This prevents unnecessary valve opening due to external factors such as wind and rain, and also ensures proper valve opening timing by cooling with condensate.
Conventional Disc Trap: Without Cap
If the jacket pressure chamber is cooled by wind or rain, the valve will open even when it should not because the closing force cannot be maintained.
Opening the valve without condensate in the chamber leads to steam loss.
Reduced steam loss and improved durability (comparison of steam loss according to weather conditions)
Steam loss due to adverse weather conditions such as rain and wind is drastically reduced by the steam jacketed pressure chamber.
A typical disc trap loses more steam when exposed to rain than under fine weather conditions. In contrast, the A3N, with no difference in steam loss due to weather, is virtually unaffected by ambient conditions.
Mirror-polished Sealing Surfaces
Some valve discs include an air leak pathway or rough finish to prevent air binding. However, this can result in greater surface wear and steam leakage due to no-load actuation. The A3N solves this problem: the bimetal air vent ring eliminates air binding and allows the hardened sealing surfaces to be mirror-polished, resulting in a tight seal that saves steam.
Long Service Life
Internal parts have been developed to provide tight sealing, which reduces wear and prolongs service life.
While a conventional disc trap generates 1.6 kg/h of steam loss when brand new and 3 kg/h after three years, the same values for the A3N are only 0.4 kg/h and 1.3 kg/h, respectively.
Bimetal air vent ring
Start-up time improvements enabled by automatic bimetal air venting
Automatic air venting reduces start-up time, greatly improving productivity. Additionally, reductions in steam loss, fuel consumption and labor can be achieved by eliminating the need for manual blowdown at start-up.
Tests indicate that by preventing air binding, the A3N can reduce start-up time by 15 minutes ‒ a reduction of approx. 60%!
How the bimetal air vent ring operates
At room temperature, the C-shaped bimetal air vent ring contracts, rising along the valve seat skirt and forcibly lifting the disc valve off its seat. With the valve open, low temperature air and condensate that enters the trap can then be discharged.
When the temperature of incoming condensate rises, the bimetal air vent ring heats up, expands, and slips down the valve seat skirt. The force keeping the valve open is released and the trap can function normally.
Increased productivity by prevention of air binding
In ThermoDyne® disc steam traps, initial air is automatically discharged by the thermostatic air venting design*, significantly reducing start-up time.
* All models except HR150A, HR260A (due to superheat temperature limits), P21S ver. C and P46S
With Bimetal Air Vent
Without Bimetal Air Vent
Easy maintenance
TLV disc traps have been designed to facilitate the replacement of just those parts affected by wear. This helps lower replacement costs and speed-up maintenance. With the replacement module, the valve disc and valve seat can easily be replaced by removing the outer and inner covers. Traps can be repaired in-line without the need for specialized equipment.
Horizontal and vertical installation possible
Disc types are known for being able to be used on both vertical and horizontal piping with no problems. However even if we install on horizontal piping, we should avoid installing the trap upside down.
Operation Animation
During startup, the trap is cold and the bimetal air vent ring is contracted, keeping the disc valve raised. During this time, large amounts of initial air and cold condensate can be discharged from the trap. The bimetal air vent ring holds the disc valve open, preventing air-flow obstacles (air binding).
As steam enters the trap, the bimetal air vent ring is heated and expands, quickly slipping down to the valve seat skirt, freeing the disc. The steam flows rapidly under the released disc and the jet creates a low-pressure region (Bernoulli's principle). The steam jet flows into the pressure chamber creating a high pressure region as the steam loses velocity and is compressed. This pressure pushes the disc valve down to close the valve seat.
When condensate enters the trap, the temperature in the pressure chamber drops, causing the steam to condense and the pressure to drop. If the pressure becomes lower than the inlet pressure, the disc valve opens to discharge condensate. Soon after the condensate is discharged, the valve closes utilizing the same principle. In this manner, the valve opens and closes automatically to intermittently discharge condensate that enters the trap.
Related projects
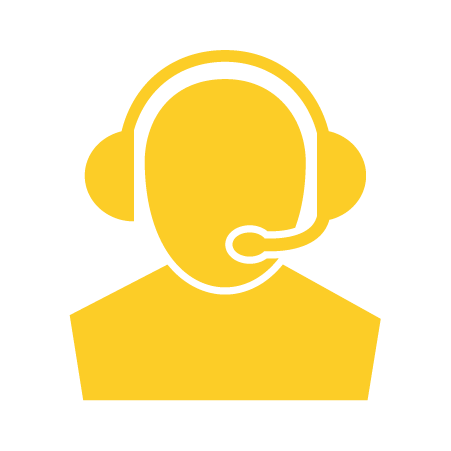
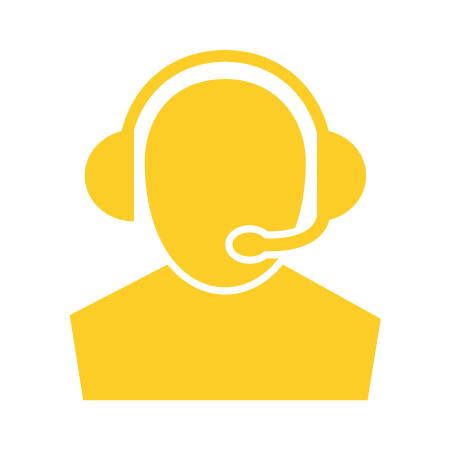
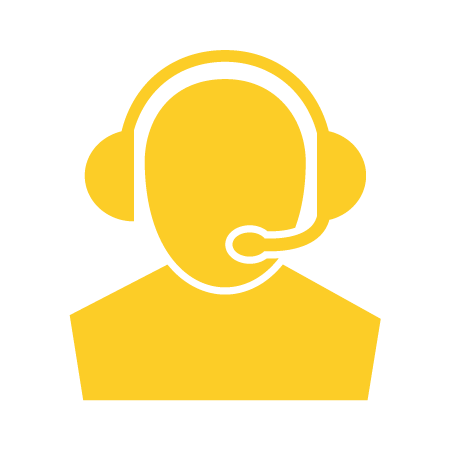
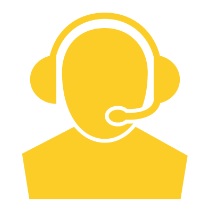
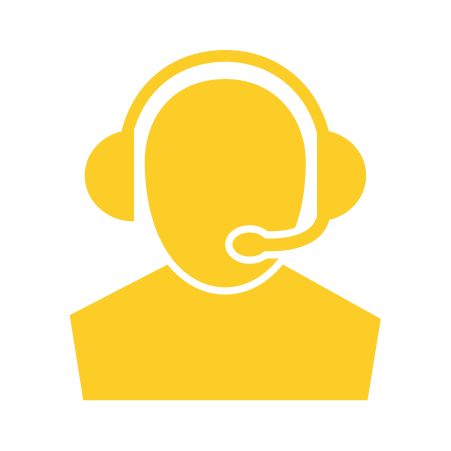