Operation Process of an Air Compressor
Operation Process of an Air Compressor
Air compressors are crucial devices in many industries, providing compressed air for various tools and equipment. Understanding the operation process of an air compressor helps ensure the efficiency and longevity of the system. Below is a detailed description of the operation process of a typical air compressor, including its main components and operational steps.
1. Basic Components of an Air Compressor
Main Components:
- Compression Element: Includes pistons or rotating vanes.
- Motor: Provides power to the compression element.
- Air Tank: Stores the compressed air.
- Inlet Valve: Allows air to enter the compressor.
- Discharge Valve: Allows compressed air to exit and enter the air tank.
- Air Filter: Removes impurities from the air before compression.
- Cooler: Reduces the temperature of the compressed air.
- Control System: Manages the operation of the compressor.
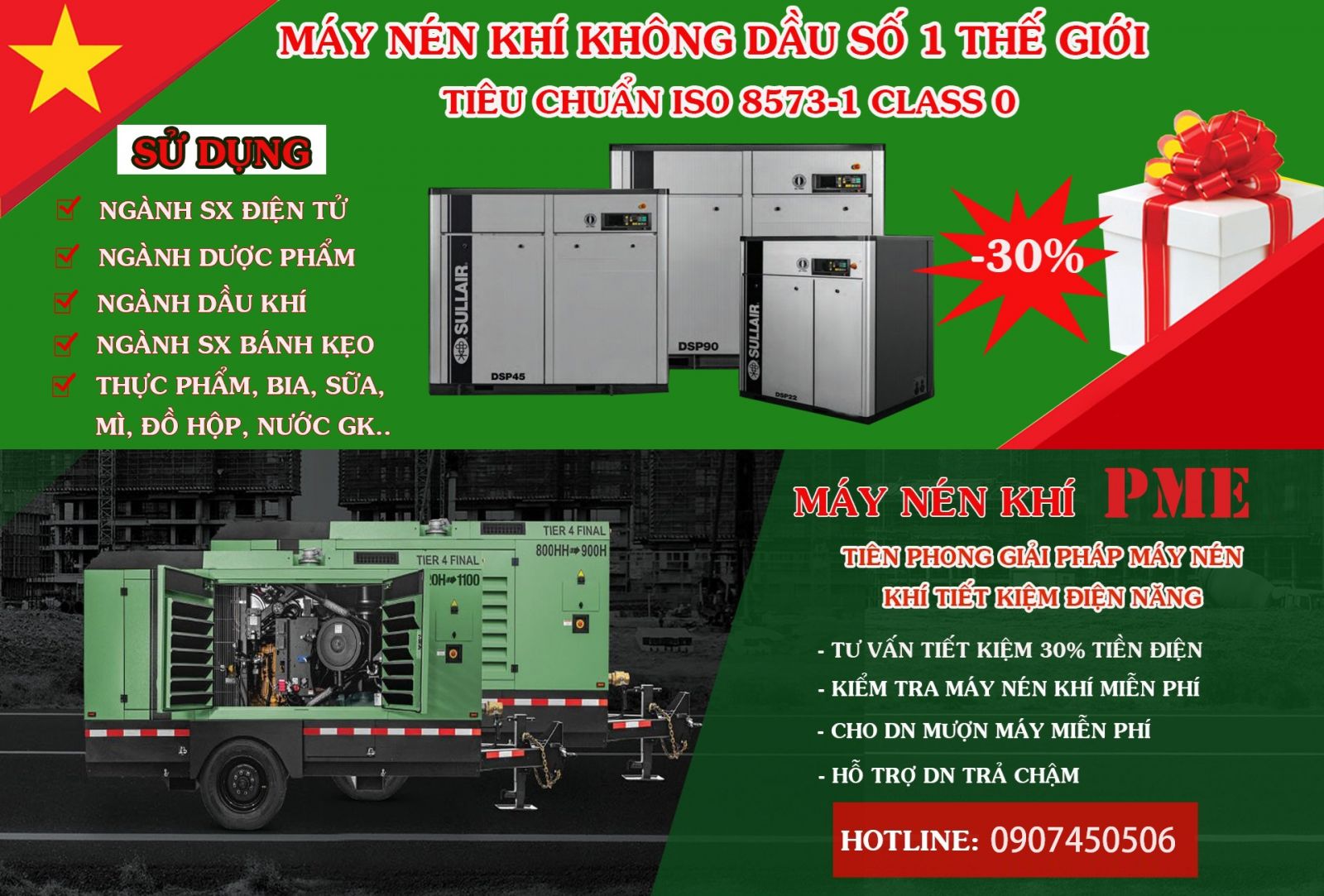
2. Operating Principle of an Air Compressor
Operation Process:
-
Air Intake (Suction):
- Opening the Inlet Valve: The inlet valve opens, allowing air from the external environment to enter the compressor.
- Air Filtration: The air passes through the air filter to remove dust and impurities before entering the compression chamber.
-
Compressing the Air (Compression):
- Motor Activation: The motor operates, providing power to the compression element.
- Compression Process: The compression element (piston or rotating vane) compresses the air, reducing its volume and increasing its pressure.
-
Discharging Compressed Air (Discharge):
- Opening the Discharge Valve: The discharge valve opens, allowing the compressed air to exit the compression chamber and enter the air tank.
- Cooling the Compressed Air: The compressed air may pass through a cooler to reduce its temperature before entering the air tank.
-
Storing and Distributing Compressed Air (Storage and Distribution):
- Storing in the Air Tank: The compressed air is stored in the air tank, ready for use.
- Distributing Compressed Air: From the air tank, compressed air is distributed through pipelines to the tools and equipment that need it.
-
Control and Regulation (Control and Regulation):
- Control System: The control system monitors the pressure and flow of compressed air, adjusting the compressor's operation to maintain stable pressure.
- Automatic On/Off: The compressor will automatically turn off when the desired pressure is reached and turn back on when the pressure drops.
3. Types of Air Compressors and Their Operating Principles
Reciprocating Compressor:
- Principle: Uses a piston moving up and down to compress the air.
- Applications: Pneumatic tools, workshop air systems.
Screw Compressor:
- Principle: Uses two rotating screws to compress the air.
- Applications: Industrial systems, manufacturing plants.
Centrifugal Compressor:
- Principle: Uses high-speed rotating impellers to compress the air.
- Applications: HVAC systems, industries requiring large air flow.
Rotary Vane Compressor:
- Principle: Uses a rotor with vanes to compress the air.
- Applications: Light industrial applications, air conditioning systems.
4. Advantages and Disadvantages of Air Compressors
Advantages:
- High Efficiency: Provides a large volume of compressed air.
- Versatility: Used in many different industrial applications.
- High Reliability: Durable and capable of continuous operation for extended periods.
Disadvantages:
- Initial Cost: High initial investment for quality compressors.
- Maintenance: Requires regular maintenance to ensure performance.
- Energy Consumption: Can consume significant energy, especially in large systems.
5. Applications of Air Compressors
Pneumatic Tools:
- Provides compressed air for tools such as jackhammers, drills, grinders, and other handheld tools in workshops and manufacturing.
HVAC Systems:
- Utilizes compressed air in HVAC systems (heating, ventilation, and air conditioning) to control temperature and air quality in buildings and industrial facilities.
Automotive Industry:
- Uses compressed air in the production processes of automobiles, from painting to assembling parts.
Food and Beverage Industry:
- Uses compressed air to operate packaging, filling, and processing equipment in the food and beverage industry.
Chemical and Pharmaceutical Industry:
- Uses compressed air in the production and packaging processes of chemicals and pharmaceuticals, ensuring safety and precision.
Oil and Gas Industry:
- Uses air compressors to transport natural gas and other gases, as well as in extraction and processing operations.
Construction Industry:
- Provides compressed air for construction equipment such as drills, compactors, and other construction tools.
Conclusion
Understanding the operation process of an air compressor is crucial to maintaining efficiency and reliability in industrial applications. By mastering how air compressors work, operators can ensure optimal performance, minimize downtime, and extend the lifespan of these essential components in industrial systems. Air compressors are not only essential tools in many industries but also play a vital role in enhancing efficiency and productivity.
Summary of Operation Process:
- Air Intake: Air is drawn in through the inlet valve and filtered through the air filter.
- Compressing the Air: The motor powers the compression element to compress the air, reducing its volume and increasing its pressure.
- Discharging Compressed Air: The compressed air is released through the discharge valve and may be cooled before entering the air tank.
- Storing and Distributing Compressed Air: The compressed air is stored in the air tank and distributed to various equipment and tools.
- Control and Regulation: The control system monitors and adjusts the pressure and flow of the compressed air to ensure stable and efficient operation.
The diverse applications of air compressors, from pneumatic tools, HVAC systems, to the automotive and construction industries, demonstrate the essential role of this equipment in improving the efficiency and productivity of various industrial sectors.
Related News
Overview Introduction to the Industrial Valve Industry in Vietnam and its Challenges
31/05/2024
Introduction to Industrial Valve Industry in Vietnam: The industrial valve industry in Vietnam is an important and indispensable part of the national industrial infrastructure. Industrial valves play a key role in controlling the flow of liquids, gases, and vapors in industrial systems. Common valve types include ball valves, gate valves, butterfly valves, pressure reducing valves, pressure regulator valves, and safety valves. These valves are widely used in many fields such as oil and gas, chemicals, water supply and drainage, food and beverage, pharmaceuticals, and energy.
Operation Process of a Pump
01/06/2024
Pumps are vital components in numerous industrial systems, used for moving fluids such as water, chemicals, oil, and other liquids. Understanding how a pump operates is essential for ensuring efficient and reliable performance. Below is a detailed description of the operation process of a typical industrial pump, including its main components and steps involved in its operation.
Operation Process of a Heat Exchanger
01/06/2024
A heat exchanger is an essential component in many industrial systems, facilitating the transfer of heat between two or more fluids without them coming into direct contact. Below is a detailed explanation of the operation process of a heat exchanger, including its main components and operational steps.
10 Most Important Industrial Equipment in Factories
01/06/2024
Modern industrial factories rely on a range of equipment to maintain high performance and ensure continuous operation. Below is a detailed description of the 10 most important types of industrial equipment, including their functions, applications, advantages, and disadvantages.
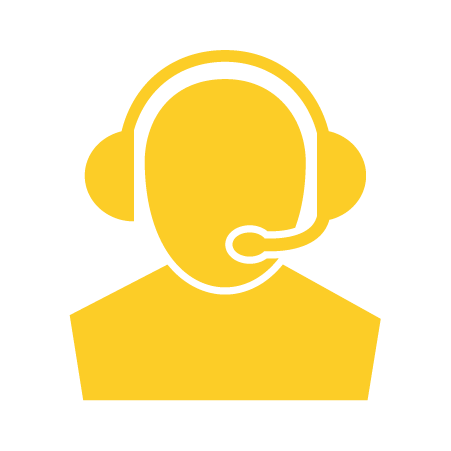
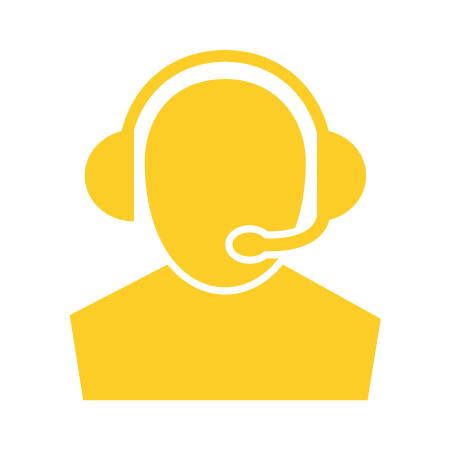
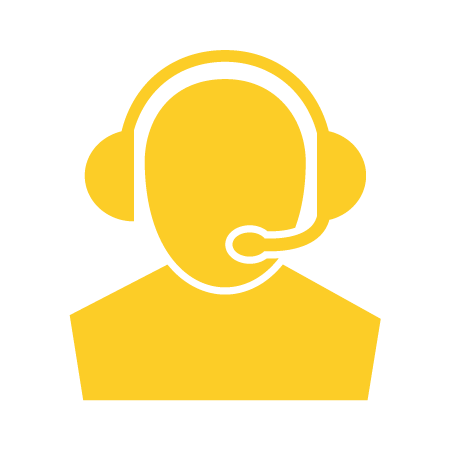
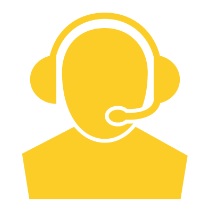
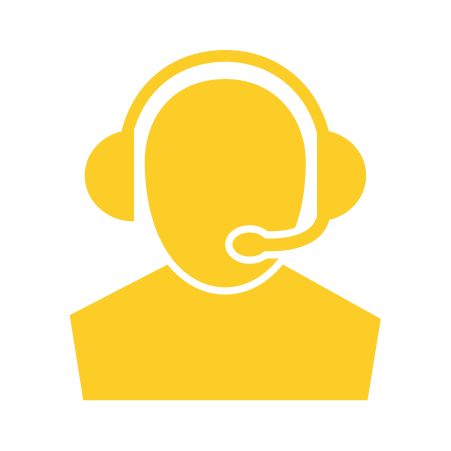