10 Most Important Industrial Equipment in Factories
10 Most Important Industrial Equipment in Factories
Modern industrial factories rely on a range of equipment to maintain high performance and ensure continuous operation. Below is a detailed description of the 10 most important types of industrial equipment, including their functions, applications, advantages, and disadvantages.
1. Industrial Pumps
Description: Industrial pumps are used to move liquids, including water, chemicals, oil, and various other fluids in industrial systems.
Function:
- Pumping and distributing liquids.
- Maintaining pressure in the system.
- Assisting in fluid and chemical processing operations.
Advantages:
- High efficiency and good durability.
- Diverse types suitable for various applications.
- Easy to maintain and repair.
Disadvantages:
- High initial investment cost.
- Requires regular maintenance to maintain performance.
- High energy consumption.
Applications:
- Oil and gas industry.
- Water and wastewater treatment.
- Food and beverage industry.
- Chemical industry.
2. Air Compressors
Description: Air compressors are mechanical devices used to increase the pressure of air by reducing its volume.
Function:
- Providing compressed air for industrial tools and equipment.
- Maintaining air pressure in systems.
- Supporting production and processing operations.
Advantages:
- High compression efficiency.
- Long lifespan and durability.
- Various power and size options.
Disadvantages:
- High energy consumption.
- Requires regular maintenance.
- Can produce noise and vibrations.
Applications:
- Manufacturing industry.
- Construction industry.
- Food and beverage industry.
- Oil and gas and chemical industries.
3. Boilers
Description: Boilers are devices that use thermal energy to produce steam or hot water for industrial processes.
Function:
- Producing steam for industrial processes.
- Providing heat for heating systems.
- Supporting production processes that require a large amount of heat.
Advantages:
- High efficiency and quick steam production.
- Diverse designs suitable for various applications.
- High durability and easy maintenance.
Disadvantages:
- High investment and operating costs.
- Requires regular maintenance and inspection.
- Safety risks if not operated properly.
Applications:
- Food and beverage industry.
- Textile industry.
- Paper and pulp industry.
- Chemical and oil and gas industries.
4. Heat Exchangers
Description: Heat exchangers are devices used to transfer heat between two or more fluids without them coming into direct contact.
Function:
- Transferring heat between fluids.
- Increasing energy efficiency in systems.
- Used in cooling and heating processes.
Advantages:
- High heat transfer efficiency.
- Flexible and diverse designs.
- Easy to maintain and clean.
Disadvantages:
- Can become clogged if the fluids contain particulates.
- High initial investment cost.
- Requires regular inspection and maintenance.
Applications:
- Oil and gas and chemical industries.
- Food and beverage industry.
- Energy industry.
- HVAC (heating, ventilation, and air conditioning) systems.
5. Wastewater Treatment Systems
Description: Wastewater treatment systems are a collection of equipment and technologies used to clean industrial wastewater before discharging it into the environment or reusing it.
Function:
- Treating and removing contaminants from wastewater.
- Ensuring wastewater meets environmental safety standards.
- Reusing water after treatment.
Advantages:
- Protecting the environment and water resources.
- Increasing water usage efficiency in industry.
- Reducing wastewater treatment costs.
Disadvantages:
- High investment and operating costs.
- Requires advanced technical and technological expertise.
- Needs continuous maintenance and operation.
Applications:
- Food and beverage industry.
- Chemical and pharmaceutical industries.
- Textile and dyeing industry.
- Paper and pulp industry.
6. Automated Control Systems
Description: Automated control systems are a collection of electronic devices and software used to monitor and control industrial production processes automatically.
Function:
- Monitoring and controlling production processes.
- Automating processes to increase efficiency.
- Collecting and analyzing production data.
Advantages:
- Increasing the accuracy and efficiency of production processes.
- Reducing human errors.
- Optimizing costs and productivity.
Disadvantages:
- High initial investment cost.
- Requires skilled personnel to operate and maintain.
- Dependence on electricity and IT systems.
Applications:
- Manufacturing industry.
- Food and beverage industry.
- Chemical and pharmaceutical industries.
- Electronics and automation industry.
7. CNC Machining Tools
Description: CNC (Computer Numerical Control) machining tools are automated mechanical devices that use computer programs to control machining processes.
Function:
- Precisely machining components.
- Creating complex and diverse products.
- Increasing productivity and reducing machining time.
Advantages:
- High precision and uniformity.
- Ability to machine complex components.
- Minimizing human errors.
Disadvantages:
- High initial investment cost.
- Requires skilled technicians to operate and program.
- Requires regular maintenance and inspection.
Applications:
- Manufacturing industry.
- Automotive and aerospace industries.
- Electronics and telecommunications industries.
- Medical and dental industries.
8. Conveyor Systems
Description: Conveyor systems are mechanical devices used to transport goods and materials within industrial factories.
Function:
- Transporting materials and products from one point to another.
- Increasing transportation efficiency and reducing production time.
- Reducing labor costs and increasing safety.
Advantages:
- Increasing productivity and transportation efficiency.
- Reducing labor costs and production time.
- Easy to integrate into existing production processes.
Disadvantages:
- High initial investment cost.
- Requires ample installation space.
- Needs regular maintenance.
Applications:
- Food and beverage industry.
- Warehousing and logistics industry.
- Electronics manufacturing industry.
- Construction and materials industry.
9. Non-Destructive Testing Equipment
Description: Non-destructive testing (NDT) equipment is used to inspect and evaluate the quality of materials and products without damaging them.
Function:
- Detecting defects in materials and products.
- Evaluating the quality and durability of products.
- Ensuring the safety and performance of equipment and structures.
Advantages:
- Inspecting and evaluating without causing damage.
- Detecting the smallest defects in materials.
- Increasing product reliability and safety.
Disadvantages:
- High investment and operating costs.
- Requires skilled technicians to perform inspections.
- Dependence on testing technology and equipment.
Applications:
- Oil and gas and chemical industries.
- Aerospace industry.
- Metal and materials manufacturing industry.
- Construction and mechanical industries.
10. Industrial Air Filtration Systems
Description: Industrial air filtration systems are devices used to remove dust, smoke, and pollutants from the air in factories and production facilities.
Function:
- Filtering and removing dust and pollutants from the air.
- Improving air quality and protecting worker health.
- Ensuring compliance with environmental standards.
Advantages:
- Improving the working environment and protecting worker health.
- Increasing production efficiency by minimizing the impact of dust and pollution.
- Easy to install and maintain.
Disadvantages:
- High investment and operating costs.
- Requires regular maintenance and filter replacement.
- Filtration efficiency may decrease over time.
Applications:
- Manufacturing industry.
- Food and beverage industry.
- Electronics manufacturing industry.
- Pharmaceutical and chemical industries.
Conclusion
The industrial equipment mentioned above plays a crucial role in ensuring the efficient and continuous operation of factories. Selecting and using the right type of equipment suitable for technical requirements and working environments is essential to achieve high performance and ensure safety in production processes. We hope this article has provided valuable information to help you better understand important industrial equipment and their applications in practice.
Contact Info:
• Phuc Minh Engineering Company Limited
• Email: info@pm-e.vn
• Tel: 028-3535.2125
• Fax: 028-3535.0254
• Web: pm-e.vn
• Address: 92/38 Street 12, Quarter 18, Binh Hung Hoa Ward, Binh Tan District, Ho Chi Minh City.
• Zalo: 0902720814 - 0907450506 - 0902800728 - 0979737351
Related News
Overview Introduction to the Industrial Valve Industry in Vietnam and its Challenges
31/05/2024
Introduction to Industrial Valve Industry in Vietnam: The industrial valve industry in Vietnam is an important and indispensable part of the national industrial infrastructure. Industrial valves play a key role in controlling the flow of liquids, gases, and vapors in industrial systems. Common valve types include ball valves, gate valves, butterfly valves, pressure reducing valves, pressure regulator valves, and safety valves. These valves are widely used in many fields such as oil and gas, chemicals, water supply and drainage, food and beverage, pharmaceuticals, and energy.
Operation Process of an Air Compressor
01/06/2024
Air compressors are crucial devices in many industries, providing compressed air for various tools and equipment. Understanding the operation process of an air compressor helps ensure the efficiency and longevity of the system. Below is a detailed description of the operation process of a typical air compressor, including its main components and operational steps. 1. Basic Components of an Air Compressor
Operation Process of a Pump
01/06/2024
Pumps are vital components in numerous industrial systems, used for moving fluids such as water, chemicals, oil, and other liquids. Understanding how a pump operates is essential for ensuring efficient and reliable performance. Below is a detailed description of the operation process of a typical industrial pump, including its main components and steps involved in its operation.
Operation Process of a Heat Exchanger
01/06/2024
A heat exchanger is an essential component in many industrial systems, facilitating the transfer of heat between two or more fluids without them coming into direct contact. Below is a detailed explanation of the operation process of a heat exchanger, including its main components and operational steps.
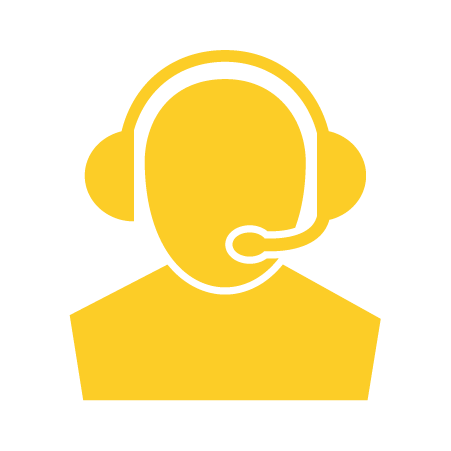
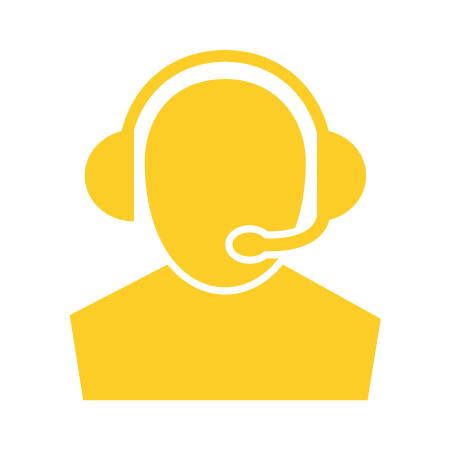
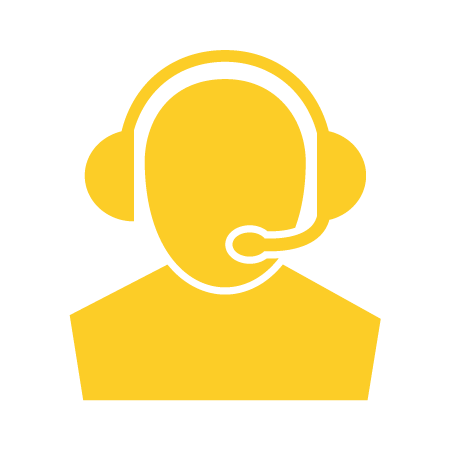
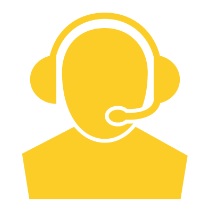
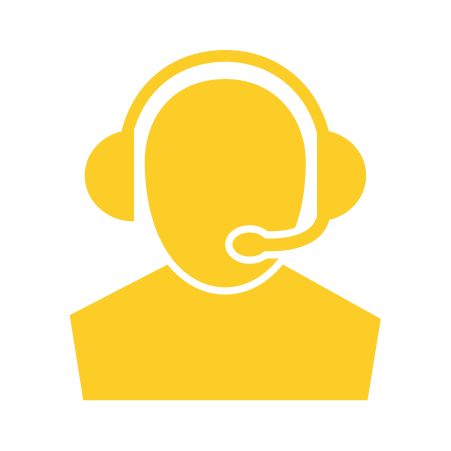