Pressure Reducing Valve
Price: Contact
Pressure Reducing Valves for Process Steam (with Built-in Separator & Trap)
DOWNLOAD CATALOG (COSPECT® Pressure Reducing Valves Pamphlet)
Troublefree Pressure Reducing Valves
COSPECT®’s built-in strainer, Super Cyclonical Effects Separator (SCE) and Free Float® steam trap help prevent scale, rust and condensate from entering the pressure reducing valve (PRV) or reaching the important interior parts.
In particular, the cyclone separator forcibly removes 98% of the condensate from the flow at the inlet side, thereby greatly reducing condensate-induced erosion of parts such as the main valve.
While the standard service life of a PRV for steam is often less than a few years, many TLV COSPECT® users are still using their COSPECT® PRVs more than 10 years after installation. Such long service life is a testimony to COSPECT®'s effectiveness in countering scale and condensate, some of the most common sources of problems for PRVs in steam systems.
Benefits and Features
-
Improved Quality of Material Being Heated
- Delivers Stable Pressure
Achieves secondary pressure accuracy within ±0.01 MPa of the set level. Even if the steam flow (load) to the equipment or the primary pressure at the pressure reducing valve changes, the Shock-Absorbing Spherical Piston (SAS) supplies steam at a constant pressure in order to prevent temperature fluctuation downstream. - Supplies Dry Steam
The built-in Cyclone Separator removes condensate from steam with a condensate separation efficiency of 98%. Condensate entrained in the steam is removed, and a strainer further removes any scale. The condensate that is separated out is discharged through the built-in Free Float® steam trap.
The increased quality of the steam contributes to improved heat conductivity.
- Delivers Stable Pressure
-
Easy to Adjust
- Pressure adjustment is simple; just use the cover cap as the adjustment spanner.
-
Long Service Life
- Rust presents a high risk to vital areas of the system. To eliminate this, all major valve components are made of stainless steel to prevent rust and corrosion. Additionally, the inclusion of a strainer in the piping installation prevents the inflow of rust and other debris, protecting the valve components and contributing to a long service life.
Application Areas
Recommended for processes requiring steam at a stable pressure and processes such as atomizers in which steam comes into direct contact with the product.
- Reactor kettles,
- Dryers,
- Heat exchangers,
- Presses,
- Steamers
- Blowers
- Atomizers, etc.
Product Details
Model | Photo | Connection | Body Material | PMO (MPaG) | TMO (°C) | Primary Pressure (MPaG) | Secondary Pressure (MPaG) | Max. Flow Capacity (kg/h) | Specifications | Manual |
---|---|---|---|---|---|---|---|---|---|---|
COS-3 |
|
Screwed | Cast Iron (FC250) |
0.3 | 220 | 0.1 - 0.3 | 0.01 - 0.05 | 950 | Specification | Contact us |
Flanged | ||||||||||
COS-16 |
|
Screwed | Cast Iron (FC250) |
1.6 | 220 | 0.2 - 1.6 | 0.03 - 1.34 | 19,800 | Specification | Contact us |
Flanged | ||||||||||
COS-21 |
|
Screwed | Ductile Cast Iron (FCD450) |
2.1 | 220 | 1.35 - 2.1 | 0.55 - 1.75 | 19,000 | Specification | Contact us |
Flanged |
- PMO = Maximum Operating Pressure
- TMO = Maximum Operating Temperature
Related projects
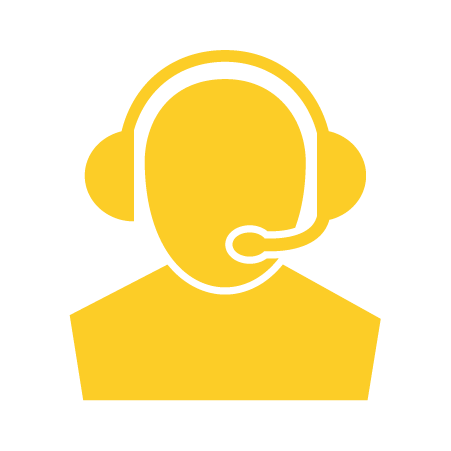
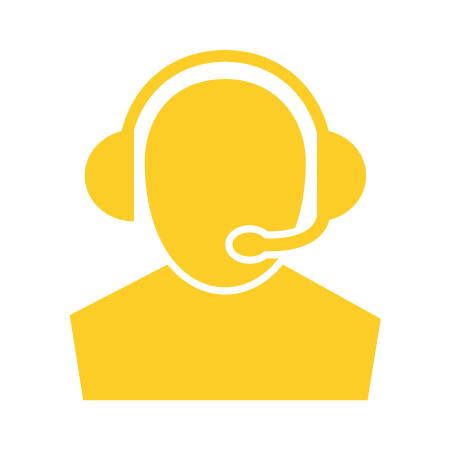
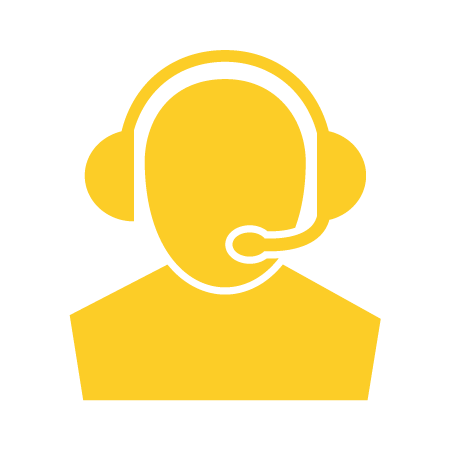
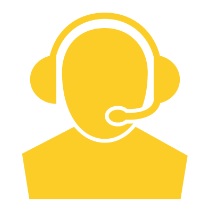
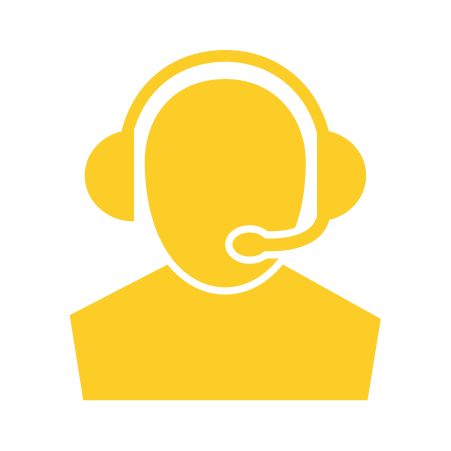