CONVAL-USA
CONVAL High Pressure Valve - USA: Specializes in supplying Globe Valves, Gate Valves, Ball Valves, Check Valves, Y-strainer, Blowdown valve, Pneumatic/Electric valve, ... with material lines of Carbon Steel, Forged Steel, Stainless Steel, Alloy, …
History

Overview
In 1962, Mr. Chester Siver completed designs for a revolutionary line of high-pressure, forged steel valves. Hamilton Standard (now Hamilton Sunstrand), a division of United Technologies Corporation, was asked to use their then-new Electron Beam Welding technology for the joining of parts into valves for subassemblies. Hamilton Standard became intrigued with the valve as an ideal application of the Electron Beam Welding technique and negotiated a contract for the rights to manufacture and sell the valve. Mr. Siver served as manager of the valve project.
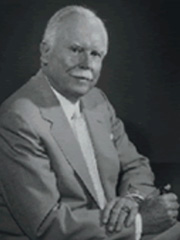
The first CLAMPSEAL® valves were introduced to the market by Hamilton Standard in 1964. However, in the mid-1960’s, growing demand for the firm’s popular aerospace products forced Hamilton Standard to make the decision to abandon its industrial products projects. The rights to the CLAMPSEAL valve reverted back to Mr. Siver. Since CLAMPSEAL® valves were born in Connecticut, Mr. Siver founded “Conval” in 1967. Today the valves are still manufactured in Connecticut, a state with a longstanding reputation for technological innovation and manufacturing excellence.
From the early years, the company has steadily expanded its product line to where it now includes: Y, Angle, and T-pattern Globe valves and Gate valves in 900 – 4500 lbs. pressure classes and 1/2″ – 4″ sizes; Whisperjets; Multiple Orifice Blowdown valves; Cryogenic and Bellows Seal valves. Today Conval is the premier manufacturer of high quality, high temperature, and high pressure forged steel valves in the world. Conval has expanded sales in Southeast Asia and developing third world countries.
Now
Conval has become a leader in providing valves for the world’s most demanding applications. We have a global team of experts to meet your most challenging needs. We invite you to contact us today. We offer high-pressure, high-temperature ball, bellows, check, gate, globe, throttling, and urea service valves.
The CLAMPSEAL® valve represents the proverbial better mouse trap. Ingeniously simple, the basic valve is comprised of only nine components. The valves are lightweight and at the same time incredibly tough and durable. Perhaps most significant of many advantages, the CLAMPSEAL® valve is much easier to renew than any other globe valve on the market. The days of use it up and throw it out have been replaced with a desire for quality, renewability, and longevity. Low acquisition cost is not as important as low life-cycle cost. Conval has benefited from this change in perspective.
Conval celebrated its 40th anniversary in 2007 with the launch of the new Camseal® Ball Valve. Sophisticated state of the art techniques are used for applying hard coatings, grinding and lapping the ball and seat of the Camseal®. The extremely high density of the coating and the precise lapping techniques produce a ball-to-seat seal that is bubble tight, and will remain bubble tight during and after installation. The Camseal® ball valve has been subjected to rigorous computer-aided analysis, laboratory testing and field testing during its development. State of the art 3-D computer modeling was used to optimize the details of the valve followed by extensive laboratory testing to verify the results. The valve has consistently passed a very rigorous program of tests.
The future is promising. Conval marked its 50th anniversary with the purchase of a 70,000 sq. ft. facility in Enfield CT. This more than doubled the manufacturing and office space of our former three building campus. We continue to develop new products to satisfy the challenging demands from industry. Inspired leadership and the innovation provided by a new generation of engineers assures our continued success.
1967-2019
Celebrating 50+ years of excellence!
Thank you for your business.
Headquarters
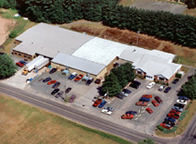
Conval Inc’s headquarters are located in Enfield, Connecticut. Conval was founded in 1967 and celebrates over 50 years of excellence.
The first CLAMPSEAL® valves were introduced to the market by Hamilton Standard in 1964. However, in the mid-1960’s, growing demand for the firm’s popular aerospace products forced Hamilton Standard to make the decision to abandon its industrial products. The rights to the CLAMPSEAL® valve reverted back to Mr. Siver. Since CLAMPSEAL® valves were born in Connecticut, Mr. Siver founded “Conval” in 1967. Today the valves are still manufactured in Connecticut, a state with a longstanding reputation for technological innovation and manufacturing excellence.
Address
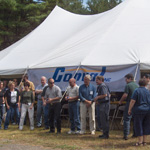
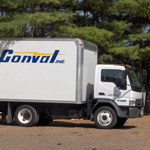
CONVAL, INC.
96 Phoenix Avenue
Enfield, CT 06082-4408
USA
Phone: 860-749-0761
Fax: 860-763-3557
Why Conval?

High Performance Valves
for the World’s Most Demanding Applications
When you buy a product you want it to work for a long time. At Conval we apply this philosophy to our high-pressure, high-temperature valves which are designed and built for extreme longevity. These are the industry’s most rugged, in-line repairable valves with the lowest lifecycle cost. As a leader in Severe Service, and specializing in extreme condition applications, all of our products exceed industry standards.
INGENIOUS DESIGN… SUPERIOR RUGGED CONSTRUCTION
Conval’s Valve line provides a modular solution to rising maintenance expenses. The cost of plant shutdown time to replace valves can be as much as or even exceed the cost of equipment.
Conval’s Valves are designed and built for extreme longevity. Features such as electroless nickel plated finish, complete material traceability of all wetted parts and yoke, instantly establish the quality of the Clampseal® Valve. The Clampseal® also has a pressure actuated backseat which provides maximum valve integrity by ensuring a positive internal stop for the valve stem and disc assembly. The actuated backseat extends packing life by securely isolating the packing from the pressure when the valve is fully open. Valves built forty years ago are still in service today.
The savings from using a Conval valve over the lifetime of a facility are substantial. Low acquisition cost is not nearly as important as low cost over the serviceable life of a valve. Maintaining a Conval valve is far easier and much less costly than replacing a competitor’s valve. Contact us today and we’ll help you get the best high-pressure, high-temperature valve for your needs.
IN-LINE RENEWABILITY
Conval Clampseal® and Camseal® Valves are much easier to renew than anything else on the market. Conval Clampseal® Valves have a secure, leak-proof bonnet which allows rapid access to valve trim for inspection and maintenance.
When inspection or servicing is required, Conval’s in-line renewable valves do not need to be cut out (as do most other welded-in valves). The result is the shortest downtime and lowest life-cycle costs in the industry. A complete service, including a reground seat, new packing or stem replacement can often be accomplished in less than thirty minutes.
GLOBE VALVE RENEWAL VS. REPLACEMENT
Repairing a globe valve involves reworking the disc and seat. Due to pipe preparation, welding, heat treating and X-ray requirements, competitor Butt Weld End valves require significantly longer change out times. The charts below exemplify the cost differences between renewing a Clampseal® Valve and replacing a competitor’s globe valve.
RENEWING A CONVAL |
||
Material |
Tool Kit |
* |
Packing |
$40.00 |
|
Subtotal |
$40.00 |
|
Labor |
Labor Rate/Hour |
$100.00 |
X Number of Hours |
2 |
|
X Number of Workers |
1 |
|
Subtotal |
$200.00 |
|
Total Renewal Cost |
$240.00 |
REPLACING A COMPETITOR’S |
||
Material |
1″, A105, Stop, Y-Globe, SW |
$1,200.00 |
Subtotal |
$1,200.00 |
|
Labor |
Labor Rate/Hour |
$100.00 |
X Number of Hours |
6 |
|
X Number of Workers |
2 |
|
Subtotal |
$1,200.00 |
|
Total Renewal Cost |
$2,400.00 |
In the example above, the cost of renewing a Clampseal® Valve is just 10% of the cost of replacing it. Renewing the packing is less than 4% of the cost of materials to replace a globe valve. In addition to the savings listed above, there are intangible savings from shorter shutdown time, which is considerable given that the cost of plant shutdown often exceeds the cost of equipment.
BALL VALVE RENEWAL VS. REPLACEMENT
Conval’s Camseal® Ball Valves are also in-line renewable. The Camseal® Valve provides zero body, seat, and stem seal leakage. The body/bonnet joint is not subject to pipeline stresses. There is no in-line body bolting to loosen and fatigue. Reliable, accurate ball alignment is achieved due to the robust engagement between the one-piece stem and the ball. The unique Camseal® replacement cartridge design makes it possible to perform in-line renewal in thirty minutes.
RENEWING A CONVAL |
||
Material |
Tool Kit |
* |
Replacement Cartridge |
$850.00 |
|
Subtotal |
$850.00 |
|
Labor |
Labor Rate/Hour |
$100.00 |
X Number of Hours |
0.5 |
|
X Number of Workers |
1 |
|
Subtotal |
$50.00 |
|
Total Renewal Cost |
$900.00 |
REPLACING A COMPETITOR’S |
||
Material |
1″, Carbon Steel WCB, SW |
$1,930.00 |
Subtotal |
$1,930.00 |
|
Labor |
Labor Rate/Hour |
$100.00 |
X Number of Hours |
6 |
|
X Number of Workers |
2 |
|
Subtotal |
$1,200.00 |
|
Total Renewal Cost |
$3,130.00 |
In the example above, the cost of renewing a Camseal® Ball Valve is just 29% of the cost of replacing a competitor’s entire valve. Add to that the savings from shorter shutdown time, and it’s clear that Conval’s valves have the lowest lifetime cost in the industry.
*Conval Tool Kit may be rented at a charge; Tool Kit may also be purchased.
Products

Globe Valve
Clampseal® Severe Service Globe Valves are tailored to exact customer requirements. Angle, T-Pattern, and Y-globe body styles available.
Gate Valve
Clampseal® Swivldisc Severe Service Gate Valves are designed for the most demanding high-pressure, high-temperature applications.
Ball Valve
Zero leakage, superior bearing support, and in-line servicing are what you can expect with these Camseal® Severe Service Ball Valves.
Strainer
Simple and rugged with a wide range of strainer element hole sizes. Socket or integral blowoff valve option available on all sizes.
Steam Whisperjet Valve
Conval Whisperjets® are designed to reduce steam pressure without causing component wear.
Piston Check Valve
Designed for severe service applications where lightweight and compact sizes are required.
Industries

Fossil Power
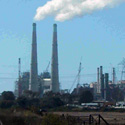
The ingenious design and rugged construction of the Conval Valve provides continuous problem free service for some of industry’s most extreme high-pressure, high-temperature applications. When servicing is required, Conval’s in-line renewable valves do not need to be cut out (as do other welded-in valves). The result is the shortest downtime and lowest life-cycle costs in the industry. A complete service, including a reground seat, new packing or stem replacement can often be accomplished in less than thirty minutes.
Users save time and money and increase plant reliability and safety by using Clampseal® and Camseal® valves due to:
Conval Feature Benefits
-
Industry’s Lowest Life Cycle Costs
-
Outage time & labor minimized
-
Leak-free shutoff minimizes repair & valve replacement
-
Longevity in extreme preset temperature services
-
Rugged leak-free bonnet seal suits actuated valve applications
-
ASME Classes through 4500 lb.
-
Reliable performance and designs
-
Wide range of alloys available
-
Variety of metallurgies
Conval Meets Unique Fossil Power Industry Requirements
-
Extreme temperature/pressure
-
Erosive flow conditions
-
Various high-cycle services
-
Many actuated valve services
Nuclear Power
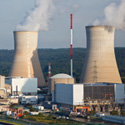
INDUSTRIES: VALVES FOR NUCLEAR POWER APPLICATIONS
Valves control flow rates, pressure, and direction, enabling functionality, safety, and control for the systems in which they operate. Valves in nuclear power plants play critical roles in both the nuclear island and the balance of plant (BOP) systems and must meet applicable Code and regulatory requirements for design, manufacture and construction to ensure safe and effective plant operation. In the United States, nuclear power plants typically fall into two categories, Boiling Water Reactors (BWR’s) and Pressurized Water Reactors (PWR’s). There are many differences between these two platforms, but in each case, valves are installed in safety-related (required for safe plant shutdown) and non-safety related applications.
-
Primary Nuclear Systems That Require Valves
Both the nuclear island and BOP systems require reliable, effective valves for safe operation, desired performance, and maintenance. Nuclear valve applications include:
MAIN STEAM SYSTEM
-
The main steam system delivers steam to the turbine and must supply this steam safely and efficiently at specified flows and pressures. Nuclear valves facilitate the following processes:
-
Regulate steam dump to condensers and steam discharge
-
Protect against Loss of Coolant Accidents (LOCA) (e.g. line break accident)
-
Protection against exceeding safe pressure levels
FEEDWATER SYSTEM
The feedwater system supplies and heats high-quality water for the reactor or steam generator, requiring precise, powerful control.
-
Control feedwater flow
-
Quickly protect condensate-feedwater piping and preheaters
CORE COOLING SYSTEM
-
The core cooling system controls the nuclear core reaction rate, requiring superior performance and reliability.
-
Protect Residual Heat Removal (RHR) pumps, and relief pumps
-
Prevent overpressure damage
-
Keep RHR and reactor coolant systems separate
-
Control flow and regulate backpressure in CVCS Chemical and Volume Control Systems
-
Halt core reactions with Safety Injection System (SIS) or Standby Liquid Control (SLC) systems
TURBINE ISLAND
-
Depending on the type of nuclear plant platform (BWR vs PWR), steam to the turbine is either contaminated (BWR) or not contaminated (PWR). In BWR’s, the turbine island is a “protected” area.The turbine island contains the turbine and auxiliary systems to convert steam from the reactor or steam generator into electricity and requires precise control to start, maintain, and shut down power generation.
-
Protection during low-capacity times such as startup, shutdown, and during load-following operation
-
Protection against overpressure and reverse flow
-
Isolation of the main steam system from other systems, including drains, and the moisture separator
AUXILIARY SYSTEMS
-
These systems are part of the BOP system to support power generation.
-
Air conditioning and ventilation
-
Compressed air
-
Demineralized water system
-
Fire protection
-
Fuel handling and storage
-
Sampling and monitoring system
-
Waste control and effluent management
VALVES USED IN NUCLEAR POWER PLANTS
We offer a selection of valves with the reliability, functionality, and performance demanded by critical nuclear power operations. Our valves offer customizable, modular valve solutions with easy interchangeability and rapid in-line repairability, providing the industry’s lowest life cycle costs.
CLAMPSEAL® GLOBE VALVES
-
Globe valves are used to regulate flow and pressure (throttle) and provide complete flow shutoff. (isolation). They are used in vent, drain, blowdown and other applications.
-
Y, angle, and T body styles
-
ASME pressure classes through 4500
-
5 standard materials, other materials available
-
Standard sizes through 4″
-
Swivldisc® Gate Valves
-
Gate valves commonly serve as isolation valves for water and steam lines, providing a lower pressure drop than globe valves. Other benefits include:
-
Swivldisc® gate design with tighter shutoff than standard gate valves for optimum sealing
-
A broad range of end connections
-
ASME pressure classes up to intermediate 3500
-
Low-emission design
-
Easy servicing with no welds or gaskets to replace due to pressure seal bonnet design
-
Body-to-bonnet joint for high integrity sealing
-
Long packing service life with fine-finished stem and packing chamber and high-performance graphite rings
CLAMPSEAL® CHECK VALVES
-
Check valves prevent reverse flow.
-
Y, T, and angle body styles
-
Lightweight, compact size
-
ASME pressure classes through 4500
-
3 standard materials, other materials available
-
Designed for high-pressure applications
-
Pressure seal bonnet allows easy servicing with no welds to cut or seals and gaskets to replace
-
Standard sizes through 4″
-
Tailored to customer requirements for installation and performance (e.g. cracking pressure)
CAMSEAL® BALL VALVES
-
Ball valves are used to isolate flow.
-
Designed for extreme high-pressure, high-temperature applications
-
Zero-leakage performance
-
ASME pressure classes through 4500
-
Standard sizes through 4″
-
Top-entry design for easy in-line maintenance for ALARA (As Low As Reasonably Achievable) compliance and cost savings
-
Metal seated for long service life
-
Forged for superior strength
STEAM WHISPERJETS
-
Whisperjets protect against damage and sonic flow created byhigh-pressure drops utilizing multi-staged trim in a designed series of pressure-reducing stages.
-
ASME pressure classes through 4500
-
Reduced component wear
-
Lowered noise level
-
Engineered/Adjustable pressure reducing multi-stage trim
-
Mitigates part erosion
-
Proven performance in high-pressure applications
-
Cost-effective pressure reduction
THE BENEFITS OF CONVAL VALVES FOR NUCLEAR APPLICATIONS
-
Our valves are ideally suited to the high-pressure, high-temperature nuclear power applications where reliability, economy, and performance are vital.
-
Industry’s lowest life cycle costs
-
Outage time & labor minimized, designs are in-line maintainable.
-
Leak-free shutoff minimizes repair & valve replacement
-
Long service life in extreme temperature services
-
Rugged leak-free bonnet seal ensures pressure boundary sealing integrity SME Classes through 4500 lb.
-
Reliable performance and designs
-
Wide range of alloys available
-
We are committed to ensuring our products are in full compliance with the strict industry requirements for the nuclear power environment. Our valves offer:
-
Nuclear Code Requirement compliance (ASME N/NPT and 10CFR50 Appendix B programs)
-
High performance
-
NUPIC audited
-
Extreme reliability
-
Ease of in-line maintenance
-
ALARA requirement compliance
CONVAL VALVES
Both our standard valves and custom valves are designed to exceed industry standards for performance and longevity in tough, high-pressure, high-temperature environments. Offering in-line
renewability and industry-leading low life cycle costs, our versatile, rugged valves are second to none. Contact us today and request a quote to take advantage of our severe service valve solutions.
Refineries
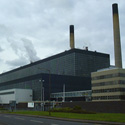
The ingenious design and rugged construction of the Conval Valve provides continuous problem free service for some of industry’s most extreme high-pressure, high-temperature applications. When servicing is required, Conval’s in-line renewable valves do not need to be cut out (as do other welded-in valves). The result is the shortest downtime and lowest life-cycle costs in the industry. A complete service, including a reground seat, new packing or stem replacement can often be accomplished in less than thirty minutes.
Users save time and money and increase plant reliability and safety by using Clampseal® and Camseal® valves due to:
Conval Feature Benefits
-
Industry’s Lowest Life Cycle Costs
-
Outage time & labor minimized
-
Leak-free shutoff minimizes repair & valve replacement
-
Longevity in extreme preset temperature services
-
Rugged leak-free bonnet seal suits actuated valve applications
-
ASME Classes through 4500 lb.
-
Reliable performance and designs
-
Wide range of alloys available
-
Variety of metallurgies
Pulp & Paper Plants
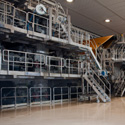
The ingenious design and rugged construction of the Conval Valve provides continuous problem free service for some of industry’s most extreme high-pressure, high-temperature applications. When servicing is required, Conval’s in-line renewable valves do not need to be cut out (as do other welded-in valves). The result is the shortest downtime and lowest life-cycle costs in the industry. A complete service, including a reground seat, new packing or stem replacement can often be accomplished in less than thirty minutes.
Users save time and money and increase plant reliability and safety by using Clampseal® and Camseal® valves due to:
Conval Feature Benefits
-
Industry’s Lowest Life Cycle Costs
-
Outage time & labor minimized
-
Leak-free shutoff minimizes repair & valve replacement
-
Longevity in extreme preset temperature services
-
Rugged leak-free bonnet seal suits actuated valve applications
-
ASME Classes through 4500 lb.
-
Reliable performance and designs
-
Wide range of alloys available
-
Variety of metallurgies
Conval Meets Unique Pulp and Paper Industry Requirements
-
Erosive services
-
Corrosive services
-
High-cycle services
-
Moderate temperature and pressures
Boilers
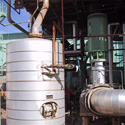
The ingenious design and rugged construction of the Conval Valve provides continuous problem free service for some of industry’s most extreme high-pressure, high-temperature applications. When servicing is required, Conval’s in-line renewable valves do not need to be cut out (as do other welded-in valves). The result is the shortest downtime and lowest life-cycle costs in the industry. A complete service, including a reground seat, new packing or stem replacement can often be accomplished in less than thirty minutes.
Users save time and money and increase plant reliability and safety by using Clampseal® and Camseal® valves due to:
Conval Feature Benefits
-
Industry’s Lowest Life Cycle Costs
-
Outage time & labor minimized
-
Leak-free shutoff minimizes repair & valve replacement
-
Longevity in extreme preset temperature services
-
Rugged leak-free bonnet seal suits actuated valve applications
-
ASME Classes through 4500 lb.
-
Reliable performance and designs
-
Wide range of alloys available
-
Variety of metallurgies
Conval Meets Unique Boiler Requirements
-
Drains and blowdowns involve high flows and frequent cycles
Cryogenic Systems
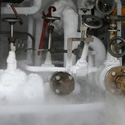
The ingenious design and rugged construction of the Conval Valve provides continuous problem free service for some of industry’s most extreme high-pressure, high-temperature applications. When servicing is required, Conval’s in-line renewable valves do not need to be cut out (as do other welded-in valves). The result is the shortest downtime and lowest life-cycle costs in the industry. A complete service, including a reground seat, new packing or stem replacement can often be accomplished in less than thirty minutes.
Users save time and money and increase plant reliability and safety by using Clampseal® and Camseal® valves due to:
Conval Feature Benefits
-
Industry’s Lowest Life Cycle Costs
-
Outage time & labor minimized
-
Leak-free shutoff minimizes repair & valve replacement
-
Longevity in extreme preset temperature services
-
Rugged leak-free bonnet seal suits actuated valve applications
-
ASME Classes through 4500 lb.
-
Reliable performance and designs
-
Wide range of alloys available
-
Variety of metallurgies
Conval Meets Unique Cryogenic System Requirements
-
Tight seals at extremely low temperatures
-
Use of metals suitable for cryogenic temperatures (Stainless Steel)
-
Extended bonnets for tight stem seal
-
Leak free actuation
-
Moderate pressures
-
Requires tight shutoff
Oil Patch Steam Injection
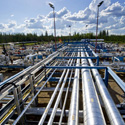
Conval’s high-pressure, high-temperature valves can withstand the needs of oil patch steam injection utilities. Conval’s engineers have worked hard to produce zero leakage valves. After being manufactured, every valve undergoes pressure testing per ASME B 16.34 to ensure that our customers get the most reliable product.
Conval Feature Benefits
-
Industry’s Lowest Life Cycle Costs
-
Outage time & labor minimized
-
Leak-free shutoff minimizes repair & valve replacement
-
Longevity in extreme preset temperature services
-
Rugged leak-free bonnet seal suits actuated valve applications
-
ASME Classes through 4500 lb.
-
Reliable performance and designs
-
Wide range of alloys available
-
Variety of metallurgies
Water Treatment
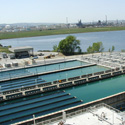
Conval’s zero leakage valves ensure water treatment facilities aren’t wasting a single drop. Our high pressure valves can be customized to meet unique requirements and to top it all off they are in line repairable.
The ingenious design and rugged construction of the Conval Valve provides continuous problem free service for some of industry’s most extreme high-pressure, high-temperature applications. When servicing is required, Conval’s in-line renewable valves do not need to be cut out (as do other welded-in valves). The result is the shortest downtime and lowest life-cycle costs in the industry. A complete service, including a reground seat, new packing or stem replacement can often be accomplished in less than thirty minutes.
Users save time and money and increase plant reliability and safety by using Clampseal® and Camseal® valves due to:
Conval Feature Benefits
-
Industry’s Lowest Life Cycle Costs
-
Outage time & labor minimized
-
Leak-free shutoff minimizes repair & valve replacement
-
Longevity in extreme preset temperature services
-
Rugged leak-free bonnet seal suits actuated valve applications
-
ASME Classes through 4500 lb.
-
Reliable performance and designs
-
Wide range of alloys available
-
Variety of metallurgies
Hydraulic Systems
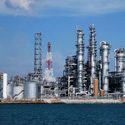
Conval’s high pressure valves can handle the intense needs of hydraulic systems. For customers who have hydraulic, electric, or pneumatic actuators, the CLAMPSEAL® valve is provided with an appropriate yoke flange and stem adapter. All actuated valves are furnished with an integral gland wrench.
The ingenious design and rugged construction of the Conval Valve provides continuous problem free service for some of industry’s most extreme high-pressure, high-temperature applications. When servicing is required, Conval’s in-line renewable valves do not need to be cut out (as do other welded-in valves). The result is the shortest downtime and lowest life-cycle costs in the industry. A complete service, including a reground seat, new packing or stem replacement can often be accomplished in less than thirty minutes.
Users save time and money and increase plant reliability and safety by using Clampseal® and Camseal® valves due to:
Conval Feature Benefits
-
Industry’s Lowest Life Cycle Costs
-
Outage time & labor minimized
-
Leak-free shutoff minimizes repair & valve replacement
-
Longevity in extreme preset temperature services
-
Rugged leak-free bonnet seal suits actuated valve applications
-
ASME Classes through 4500 lb.
-
Reliable performance and designs
-
Wide range of alloys available
-
Variety of metallurgies
Applications

Variable Tandem Blowdown Valve
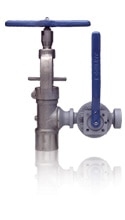
Unlike older massive designs with limited serviceability, the CLAMPSEAL® unit tandem valve offers compactness, lighter weight and easy maintainability as well as longevity of service.
Traditional bottom blowdown service requires a tandem valve. Unlike older massive designs with limited serviceability, the CLAMPSEAL® unit tandem valve offers compactness, lighter weight and easy maintainability as well as longevity of service. These valves are suitable for steam drains or any high pressure letdown service.
-
Industry’s Lowest Life Cycle Costs
-
High-performance Packing System
-
Zero Seat Leakage
Standard Size
Sizes through 4″”
Pressure Rating
ASME Class through 4500 #
Standard Forging ASME Materials
SA 105, SA 182-F22, SA 182-F91, SA 182-F92, SA 182-F316
Connections
Socket Weld, Butt Weld, Clamp Connector
Accessories
Actuators – electric, pneumatic, or hydraulic
Limit switch – single or double
Locking devices – open, closed, both
Position indicator
Stem shroud
DESIGN FEATURES
Pressure Seal Bonnet
The simple and effective pressure seal bonnet provides ready access for servicing with no welds to cut or seal rings or gaskets to replace. The body-to-bonnet joint integrity is maintained through countless thermal cycles.
Single-piece Gland
In extreme environments, the simpler the design and the fewer the parts, the better. The durable single-piece stainless steel gland contributes to the longevity of the valve.
Axial-Loaded Packing System
The Axial design ensures tight concentricity, which eliminates side loading of the packing and minimizes wear forces on the trim components. This feature is critical for superior valve performance.
Pressure-Actuated Backseat
The Clampseal® pressure-actuated backseat provides maximum valve integrity by ensuring a positive internal stop for the valve stem and disc assembly. The pressure actuated backseat also extends packing life by securely isolating the packing from the pressure when the valve is fully open.
Rapid In-Line Renewability
The CLAMPSEAL® Valve is much easier to renew than anything else on the market. The CLAMPSEAL® Valve line provides a modular solution to rising maintenance expenses. Low acquisition cost is not as important as low cost over the serviceable life of a valve. Maintaining a Conval valve is far easier and much less costly than replacing a competitor’s valve.
Three Way Service Valve
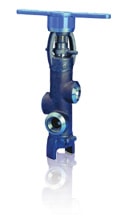
Conval has responded to the need for a high pressure, high temperature three-way valve with easy serviceability for both seats.
Conval has responded to the need for a high pressure, high temperature 3-way valve with easy serviceability for both seats. Excellent service history and versatility make the CLAMPSEAL® valve the choice for 3-way service.
-
Industry’s Lowest Life Cycle Costs
-
High-performance Packing System
Standard Sizes
Sizes through 4”
Pressure Rating
ASME Class through 4500 #
Standard Casting ASME Materials
SA-216 Gr. WCB, SA-217 Gr. WC9, SA-217 Gr. 12A, SA-351 Gr. CF8M
Connections
Socket Weld, Butt Weld, Flanged End, Clamp Connector
Accessories
Actuators – electric, pneumatic, or hydraulic
Limitswitch – Single or double
Locking Devices – open, closed, or both
Position Indicator
Stem Shroud
DESIGN FEATURES
Pressure Seal Bonnet
The simple and effective pressure seal bonnet provides ready access for servicing with no welds to cut or seal rings or gaskets to replace. The body-to-bonnet joint integrity is maintained through countless thermal cycles.
Single-piece Gland
In extreme environments, the simpler the design and the fewer the parts, the better. The durable single-piece stainless steel gland contributes to the longevity of the valve.
Axial-Loaded Packing System
The Axial design ensures tight concentricity, which eliminates side loading of the packing and minimizes wear forces on the trim components. This feature is critical for superior valve performance.
Pressure-Actuated Backseat
The Clampseal® pressure-actuated backseat provides maximum valve integrity by ensuring a positive internal stop for the valve stem and disc assembly. The pressure actuated backseat also extends packing life by securely isolating the packing from the pressure when the valve is fully open.
Rapid In-Line Renewability
The CLAMPSEAL® Valve is much easier to renew than anything else on the market. The CLAMPSEAL® Valve line provides a modular solution to rising maintenance expenses. Low acquisition cost is not as important as low cost over the serviceable life of a valve. Maintaining a Conval valve is far easier and much less costly than replacing a competitor’s valve.
Naval Boiler Blowdown Valve
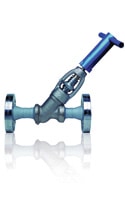
The CLAMPSEAL® Naval Boiler Blowdown valve meets the requirements of MIL-V-17737 and other applicable specifications.
The CLAMPSEAL® Naval Boiler Blowdown valve is qualified to meet the requirements of MIL-V-17737 and other applicable specifications.
-
Industry’s Lowest Life Cycle Costs
-
High-performance Packing System
-
Qualified to meet MIL-V-17737 Requirements
Standard Size
1-1/2”
Type
I (Handwheel) or II (T-handle)
Pressure Rating
ASME Class 600 # or 1500 #
Style
Y or Angle Pattern
Standard Materials
Carbon Steel or Alloy Steel
Per Catalog
NSN
4820-01-124-3694, 4820-01-140-4834, 4820-01-018-3780, 4820-01-018-3781
Urea Service Valve
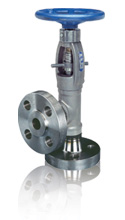
Conval Clampseal® Severe Service Urea Valves are designed for high-pressure piping of urea reactors, strippers, and condensers.
-
Industry’s Lowest Life Cycle Costs
-
Interchangeable Modular Body Styles
-
Pressure-actuated Backseat
-
High-performance Packing System
Standard Sizes and Configurations
Sizes through 6″
Configurations Include
Globe (Y-Pattern, T-Pattern, and Angle Styles), Gate, Check (Piston and Axial Styles), and Camseal Top Entry Ball Valves
Pressure Rating
ASME Class through 2500#
Standard Materials
UNS S31050 (25-22-2), F53, Ferralium 255, 316L, 316L Urea Grade, others as specified
Connections
Flanged End, (Raised Face, Lens Ring, Ring Type Joint) Hub Connector, Butt Weld, Socket Weld, others as specified
Accessories
Actuators – Electric, Pneumatic, Hydraulic
Locking Device – Open, Closed, Both
Limit Switch – Single or Dual
Position Indicator
Design Features
Conval Severe Service valves are designed for best in class service life and in-line reparability
Pressure-actuated Backseat
The Clampseal® pressure-actuated backseat provides maximum valve integrity by ensuring a positive internal stop for the valve stem and disc assembly. The pressure actuated backseat also extends packing life by securely isolating the packing from the pressure when the valve is fully open.
Axial-loaded Packing System
The axial design ensures tight concentricity, which eliminates side loading of the packing and minimizes wear forces on the trim components. This feature is critical for superior valve performance.
Urea Synthetization Applications
Conval urea service valves applications include high-pressure piping of urea reactors, strippers and condensers. Our valves are designed for use with ammonium carbamate, nitric acid, ammonia, and other urea process fluids. Designs include provisions for self-draining waterways and the elimination of collection points where the corrosive media (e.g. ammonium carbamate) can stagnate resulting in crevice corrosion and subsequent cracking.
Throttling Valve

Conval Clampseal® Throttling Valves are designed for a wide range of severe service applications requiring repeatable flow control and dependable shutoff.
-
Industry’s Lowest Life Cycle Costs
-
Replaceable Seat/Venturi
-
Low Velocity Across Main Seat
-
Precise Flow Control
-
Pressure Seal Bonnet
-
Best Shutoff in Industry
Standard Sizes
Sizes through 4″
Pressure Rating
ASME Class through 4500 #
Standard Forging ASME Materials
SA 105, SA 182-F22, SA 182-F91, SA 182-F92, SA 182-F316
Other materials available upon request
Accessories
Actuators – Air, Motor, Hydraulic
Limitswitch – Single or double
Locking Devices – open, closed, or both
Position Indicator
Stem Shroud
THROTTLING VALVE DESIGN FEATURES
Replaceable 4400 Stainless Steel Seat/Venturi
The venturi is an integral part of the removable seat. It is easily changed in-line should different flow characteristics be required or replacement be necessary from excessive wear. The orifice is sized to keep fluid velocity across the seat below damaging levels. The exit orifice angle is designed to minimize downstream piping erosion and noise. Several erosion-resistant materials are available. Consult factory.
Position Indicator
The position indicator is easy to read and an accurate indication of valve stem position.
Axially-loaded Packing System
The Axial design ensures tight concentricity, which eliminates side loading of the packing and minimizes wear forces on the trim components. This feature is critical for superior valve performance.
Mated Stem Assembly
The stem assembly is mated to the orifice for proper control. Like the orifice seat assembly, it is easily changeable should different flow characteristics be required or excessive erosion or corrosion be a problem.
Pressure Seal Bonnet
The simple and effective pressure seal bonnet provides ready access for servicing with no welds to cut or seal rings or gaskets to replace. The body-to-bonnet joint integrity is maintained through countless thermal cycles.
Single-piece Gland
In extreme environments, the simpler the design and the fewer the parts, the better. The durable single-piece stainless steel gland contributes to the longevity of the valve.
Pressure-Actuated Backseat
The Clampseal® pressure-actuated backseat provides maximum valve integrity by ensuring a positive internal stop for the valve stem and disc assembly. The pressure actuated backseat also extends packing life by securely isolating the packing from the pressure when the valve is fully open.
Rapid In-Line Renewability
The CLAMPSEAL® Throttling Valve is much easier to renew than anything else on the market. The CLAMPSEAL® Valve line provides a modular solution to rising maintenance expenses. Low acquisition cost is not as important as low cost over the serviceable life of a valve. Maintaining a Conval valve is far easier and much less costly than replacing a competitor’s valve.
Bellow Seal Valve
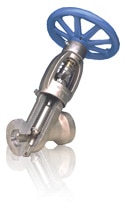
Conval Bellows Seal Valves meet all of the rigorous requirements of MSS SP-117, ensuring bellows longevity.
-
Industry’s Lowest Life Cycle Costs
-
Fugitive Emissions Sealing
-
High Cycle Bellows
-
In-Line Servicing
-
High Flow Capacity
Bellows seal valves are valves employed in piping systems to safeguard against leakage. When selected and installed properly, they minimize the risk of potentially harmful chemicals causing injury or illness to workers and damage to the surrounding environment.
Standard Bellows Seal Sizes
Sizes through 4”
Pressure Rating
Through ASME Class through 2500 #
Standard Forging ASME Materials
SA 105, SA 182-F22, SA 182-F91, SA 182-F92, SA 182-F316
Other materials available upon request.
Accessories
Actuators – Electric, Pneumatic or Hydraulic
Locking Devices – Open, Closed or Both
Limit Switches – Single or Dual
Stem Shroud
Position Indicator
Leak-Off Port
BELLOWS SEAL DESIGN FEATURES
Conval Bellows Seal Valve vs. Packed Valves
Packed valves require two seal boundaries: a 360° seal on the stem surface and a 360° seal on the stuffing box wall. The Conval bellows seal valve removes these two leak paths. Conval bellows seal valves are used when packed valves may not reliably contain light gases or hazardous system fluids. In all applications, the 6-ply Inconel®, welded bellows stem seal is more reliable than sliding stem seals.
Zero Fugitive Emissions
Every Conval bellows assembly is tested for zero leakage using a helium gas mass spectrometer before undergoing further shell and seat leakage testing. Conval’s bellows seal emits no detectable leakage, well beyond Method 21 Fugitive Emissions Test Protocol.
No Torsion of the Bellows
A robust rising, non-rotating stem system prevents destructive torsion, providing extremely long service life from the advanced bellows design.
Three Body Styles
Conval bellows seal valves are available in Y-pattern, Angle-pattern, and T-pattern body styles.
Low Operating Torque
The manual bellows seal valve is provided with a rugged bearing system and grease fitting to minimize operating torque over the life of the valve.
Double Back-up Seating
In the full open position, Conval bellows seal valves are equipped with a superior backseat, isolating a secondary stem seal from the process fluid. The graphitic stem seal is precisely loaded by Conval’s balanced axial gland and Integral Gland Wrench (IGW), providing superb sealing to back up the bellows.
Extended Seat Life
Positive shut-off is achieved over a very long operational life due to the solid cobalt-chrome seats and discs, even in high cycle and high fluid velocity services. A cobalt-free option is available for nuclear and chemical applications.
Flexibility of Design
Conval offers a double height bellows which provides the highest bellows valve flow capacity (Cv) available per pipe size. Test ports (with lantern gland) may also be specified.
Axially-loaded Packing System
The Axial design ensures tight concentricity, which eliminates side loading of the packing and minimizes wear forces on the trim components. This feature is critical for superior valve performance.
Pressure Seal Bonnet
The simple and effective pressure seal bonnet provides ready access for servicing with no welds to cut or seal rings or gaskets to replace. The body-to-bonnet joint integrity is maintained through countless thermal cycles.
Single-piece Gland
In extreme environments, the simpler the design and the fewer the parts, the better. The durable single-piece stainless steel gland contributes to the longevity of the valve.
Pressure-Actuated Backseat
The Clampseal® pressure-actuated backseat provides maximum valve integrity by ensuring a positive internal stop for the valve stem and disc assembly. The pressure actuated backseat also extends packing life by securely isolating the packing from the pressure when the valve is fully open.
Rapid In-Line Renewability
The CLAMPSEAL® Valve is much easier to renew than anything else on the market. The CLAMPSEAL® Valve line provides a modular solution to rising maintenance expenses. Low acquisition cost is not as important as low cost over the serviceable life of a valve. Maintaining a Conval valve is far easier and much less costly than replacing a competitor’s valve.
HOW DO BELLOWS SEAL VALVES WORK?
These valves feature an accordion like bellows—i.e., the bellows cartridge component, welded to the valve stem and bonnet. During the valve stroke the bellows compress or expand along with the sliding stem’s linear motion with little to no friction.
TYPES OF BELLOWS
-
Formed bellows: Conval’s standard design, formed bellows begin as flat sheet (thin wall foil) rolled into a tube and fusion-welded longitudinally forming a single layer. Thin metal layers are combined to form multi-ply bellows. Mechanical or hydrostatic force forms the bellows with wide-spaced rounded folds. Conval has supplied bellows with as many as 6 plies for higher pressure applications.
-
Welded bellows: Welded bellows are manufactured by welding washer-like plates of thin metal at both their inner and outer circumferences.
TYPES OF BELLOWS SEAL VALVES
Gate valves, globe valves and ball valves may all be supplied with Bellows should the application require.
APPLICATIONS OF BELLOWS SEAL VALVES
These critical components are an essential part of safe fluid system operation in a broad range of industries, including the following:
-
Aerospace
-
Biotechnology
-
Chemical processing
-
Fossil power
-
Nuclear power
-
Petroleum
-
Pharmaceutical
-
Semiconductor manufacturing
-
Vacuum and ultra-high vacuum
FAQS
Below we provide answers to some of the most frequently asked questions (FAQs) regarding bellows seal valves.
What are some advantages of using bellows seal valves?
The primary function of bellows seal valves is preventing potentially harmful or toxic fugitive emissions which can negatively affect unprotected humans and the surrounding environment. In addition to reducing the risk to employees or the environment, these valves decrease the amount of material lost during operations, which translates to lower overall material costs and greater throughput.
How do I choose a bellows seal valve?
When selecting a bellows seal valve for a system, there are several factors to keep in mind. Some of the key design considerations are:
-
The valve material chosen should be compatible with the operating conditions of the system, including the fluid media, temperature, and pressure. Common materials employed include stainless steel and nickel-based super alloys.
-
Pressure rating. The valve should be rated to handle the range of pressures and temperatures expected from the fluid system. Typical ratings range from ASME 150 to 2500 class.
-
Design Qualifications. Ensure the bellows is qualified to industry standards such as EPRI, MSS, API, or ISO.
-
The size of the valve should suit the design of the system. Conval bellows seal valves are available in sizes ranging from ¼ inch through 4 inch NPS.
How to prevent bellows seal valves from failing
Bellows seal valves are built for reliable operation. While rare, failures do occur. Generally, the root cause of the failure stems, not from the quality of the valve or bellows, but from improper selection, installation, or operation. Some guidelines for avoiding valve failure include:
-
Monitor for excessive back pressure or high inlet pressure variations
-
Select properly sized valves and bellows
-
Operate within the design pressure, temperature and stem stroke ranges.
-
Prevention of cavitation, flashing and other unusual damaging flow conditions.
CONTACT THE VALVE EXPERTS AT CONVAL, INC. TODAY
For all your bellows seal valve needs, turn to the valve experts at Conval, Inc. Since our founding in 1967, we have developed a reputation as a premier manufacturer of high-pressure/temperature, forged steel valves suitable for use in the most demanding severe service applications. Our commitment to quality translates to our products’ superior durability and performance at the lowest life-cycle cost in the industry.
For additional information about our valve offerings or assistance specifying one (or hopefully many) for your application, contact us today.
Feedwater Pump Recirculation Bypass Valve
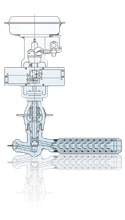
Conval Clampseal® Recirculation Bypass Valves are designed to prevent overheating of feedwater pumps during critical low-load operating periods.
-
Industry’s Lowest Life Cycle Costs
-
High Pressure Drop
-
Flexible Number of Whisperjet Stages
-
Prevent Feedwater Pump Overheating
-
Save Component Wear
-
Quickly Configured to User’s Specifications
Standard Sizes
Sizes through 4″
Pressure Rating
ASME Class through 4500 #
Standard Forging ASME Materials
SA 105, SA 182-F22, SA 182-F91, SA 182-F92, SA 182-F316
Connections
SW, BW Ends
Patterns
Angle, Y or T pattern
Accessories
Actuators – Air, Motor, Hydraulic, Manual
Limitswitch – Single or double
Locking Devices – open, closed, or both
Position Indicator
Stem Shroud
DESIGN FEATURES
Leak-proof Bonnet/Chamber
A secure, leak-proof bonnet allows rapid access to valve trim for inspection and maintenance.
Pressure Actuated Backseat
The Clampseal® pressure-actuated backseat provides maximum valve integrity by ensuring a positive internal stop for the valve stem and disc assembly. The pressure actuated backseat also extends packing life by securely isolating the packing from the pressure when the valve is fully open.
Pressure Seal Bonnet
The simple and effective pressure seal bonnet provides ready access for servicing with no welds to cut or seal rings or gaskets to replace. The body-to-bonnet joint integrity is maintained through countless thermal cycles.
Single-piece Gland
In extreme environments, the simpler the design and the fewer the parts, the better. The durable single-piece stainless steel gland contributes to the longevity of the valve.
Axial-Loaded Packing System
The Axial design ensures tight concentricity, which eliminates side loading of the packing and minimizes wear forces on the trim components. This feature is critical for superior valve performance.
Rapid In-Line Renewability
The CLAMPSEAL® Valve is much easier to renew than anything else on the market. The CLAMPSEAL® Valve line provides a modular solution to rising maintenance expenses. Low acquisition cost is not as important as low cost over the serviceable life of a valve. Maintaining a Conval valve is far easier and much less costly than replacing a competitor’s valve.
Cryogenic Valve
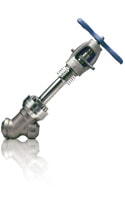
The CLAMPSEAL® delivers tight shutoff and operability through a wide temperature range and meets ANSI B 31.3 requirements.
High pressure cryogenic service demands special attention to design and quality of material and fabrication. The CLAMPSEAL® delivers tight shutoff and operability through a wide temperature range and meets ASME B 31.3 requirements.
-
Industry’s Lowest Life Cycle Costs
-
Metal-to-Metal Pressure Seal Bonnet
-
Single-piece Gland
-
Tight Shut-off
-
In-line Servicing
Standard Sizes
Sizes through 4″
Pressure Rating
ASME through 2500 #
ASME B31.3, ASME B16.34
Special pressure classes available
Standard Materials
Forged Stainless Steel SA 182-F316
Special materials available
Connections
SW and BW Ends
Special ends available
DESIGN FEATURES
Pressure Seal Bonnet
The simple and effective pressure seal bonnet provides ready access for servicing with no welds to cut or seal rings or gaskets to replace. The body-to-bonnet joint integrity is maintained through countless thermal cycles.
Single-piece Gland
In extreme environments, the simpler the design and the fewer the parts, the better. The durable, single-piece stainless steel gland contributes to the longevity of the cryogenic valve.
Axial-Loaded Packing System
The Axial design ensures tight concentricity, which eliminates side loading of the packing and minimizes wear forces on the trim components. This feature is critical for superior valve performance.
Pressure-Actuated Backseat
The Clampseal® pressure-actuated backseat provides maximum valve integrity by ensuring a positive internal stop for the valve stem and disc assembly. The pressure actuated backseat also extends packing life by securely isolating the packing from the pressure when the valve is fully open.
Rapid In-Line Renewability
The CLAMPSEAL® Valve is much easier to renew than anything else on the market. The CLAMPSEAL® Valve line provides a modular solution to rising maintenance expenses. Low acquisition cost is not as important as low cost over the serviceable life of a valve. Maintaining a Conval valve is far easier and much less costly than replacing a competitor’s valve.
Fire Safe Valve
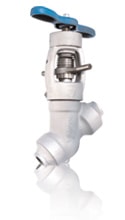
Conval Clampseal® Fire-Safe Valves are ideal for refining and chemical plants where fire safety is a major concern.
-
Industry’s Lowest Life Cycle Costs
-
Exceeds API Standard 6FA
-
Retrofit with any Clampseal® Globe Valve
-
Single-piece Gland
-
Cartridge-type Packing Chamber
-
Pressure Assisted Backseat
Standard Sizes
Sizes through 4″
Pressure Rating
ASME Class through 2500 #
Standard Materials
A105, F22, F91, F92, F316, F347, InconelTM, MonelTM and other materials.
Connections
SW and BW Ends
Special ends available
Accessories
Actuators – electric, pneumatic, or hydraulic
Limitswitch – Single or double
Locking Devices – open, closed, or both
Position Indicator
Stem Shroud
Special Testing
Tested and passed API Standard 6FA
DESIGN FEATURES
Meets API Standard 6FA by extremely high margins
In a typical globe valve, if the yoke is exposed to the direct flame of a fire, it will expand at a rate much greater than the stem. Thermal effects cause the yoke arms to grow, which makes the disc lift up off the seat, leading to considerable leakage. This is true of virtually all globe valves now on the market.
Conval has developed a simple mechanism that compensates for thermal expansion. The stem bushing is allowed to float in a recess in the top of the yoke and is loaded by a series of Belleville washers. The Bellevilles maintain a load, forcing the stem assembly down into the seat, even when the yoke expands at the high temperatures of a refinery or chemical fire.
The Conval fire-safe Clampseal® valve has been tested and successfully passed the rigorous test procedure defined by the American Petroleum Institute (API) Standard 6FA. In brief, this procedure calls for the test valve to be placed in line and pressurized to 75% of rated pressure, then subjected to a 1400-1800°F fire for 30 minutes. The valve is then quenched with water to cool it to ambient temperature, cycled to prove operability, and then subjected to further pressure testing. The valve is required to maintain strict leakage allowances during and after the burn.
Retrofitted with Standard Clampseal® Globe Valves
Our entire line of Clampseal® globe valves may be retrofitted with this fire-safe capability, including: Y-pattern stop and stop check valves; T-pattern stop and stop check valves; angle pattern and stop check valves.
Single-piece Gland
In extreme environments, the simpler the design and the fewer the parts, the better. The durable single-piece stainless steel gland contributes to the longevity of the valve.
Cartridge-type Packing Chamber
With secure leak-proof bonnet, this chamber allows rapid access to valve trim for inspection and maintenance. Pressure boundary is sealed at the smallest diameter possible, to ensure maximum strength and low stress.
Pressure-Actuated Backseat
The Clampseal® pressure-actuated backseat provides maximum valve integrity by ensuring a positive internal stop for the valve stem and disc assembly. The pressure actuated backseat also extends packing life by securely isolating the packing from the pressure when the valve is fully open.
Pressure Seal Bonnet
The simple and effective pressure seal bonnet provides ready access for servicing with no welds to cut or seal rings or gaskets to replace. The body-to-bonnet joint integrity is maintained through countless thermal cycles.
Axial-Loaded Packing System
The Axial design ensures tight concentricity, which eliminates side loading of the packing and minimizes wear forces on the trim components. This feature is critical for superior valve performance.
Rapid In-Line Renewability
The CLAMPSEAL® Valve is much easier to renew than anything else on the market. The CLAMPSEAL® Valve line provides a modular solution to rising maintenance expenses. Low acquisition cost is not as important as low cost over the serviceable life of a valve. Maintaining a Conval valve is far easier and much less costly than replacing a competitor’s valve.
Hiltap SaVD Series Safe Vent Drain
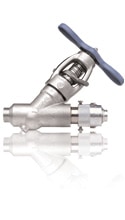
Now you can order a simple, single-weld, dual sealing system to Clampseal® Y-pattern valves to enhance leak-free performance and allow for fast, safe, environmentally-friendly venting and draining of piping systems.
-
Industry’s Lowest Life Cycle Costs
-
Pressure Assisted Bonnet
-
Self-aligning Metal Seat
-
Pressure-activated HILTAP®
-
Solid Cobalt Valve Seat and Disc
-
Replaceable Packing Chamber
Standard Sizes
3/4″ through 1 1/2″
Pressure Rating
ASME Class through 2500 #
Standard Forging ASME Materials
SA 105, SA 182-F22, SA 182-F91, SA 182-F92, SA 182-F316
Connections
NPT, BW, SW Ends
Patterns
Y Pattern
Standard Options
Securing chain
DESIGN FEATURES
Pressure Assisted Bonnet
Combined with self-aligning solid metal-to-metal seat and disc, this provides effective sealing without welds or gaskets.
Pressure Activated HILTAP®
The backseat requires low torque for total isolation of packing.
Replaceable Packing Chamber
The replaceable packing chamber allows for fast repacking of any valve.
Secondary Containment
The HILTAP® metal-to-metal connector is the secondary containment. It includes two dynamic sealing surfaces, a compact profile, ultra-safe residual pressure venting, and the ability to quickly connect to a gravity drain hose. The coupling locks under line pressure.
Easy Installation and Cleaning
Just one weld is required to connect to a pipe. Fitting is machined as an integral part of the valve. Locking threads are located outside wetted volumes. Valve-mounted couplings can be steam cleaned and pressure-purged.
Single-Drip Depressurization
Safe depressurization is achieved in just one drip of fluid, significantly enhancing safety and environmental protection.
No-Spill Gravity Drainage
Hooking up the Safe Vent Drain with a matching HILTAP® drainage pipe is safe, reliable, and quick. This minimizes downtime, labor, and environmental cleanup expense.
Meets OSHA Regulations
The HILTAP SaVD Series Safe Vent Drain replaces low pressure bull plugs and screwed caps. It is manufactured to ISO 9001-2000. Full material traceability, technical specifications, and CRN registration are available upon request.
Pressure Seal Bonnet
The simple and effective pressure seal bonnet provides ready access for servicing with no welds to cut or seal rings or gaskets to replace. The body-to-bonnet joint integrity is maintained through countless thermal cycles.
Single-piece Gland
In extreme environments, the simpler the design and the fewer the parts, the better. The durable single-piece stainless steel gland contributes to the longevity of the valve.
Axial-Loaded Packing System
The Axial design ensures tight concentricity, which eliminates side loading of the packing and minimizes wear forces on the trim components. This feature is critical for superior valve performance.
Pressure-Actuated Backseat
The Clampseal® pressure-actuated backseat provides maximum valve integrity by ensuring a positive internal stop for the valve stem and disc assembly. The pressure actuated backseat also extends packing life by securely isolating the packing from the pressure when the valve is fully open.
Rapid In-Line Renewability
The CLAMPSEAL® Valve is much easier to renew than anything else on the market. The CLAMPSEAL® Valve line provides a modular solution to rising maintenance expenses. Low acquisition cost is not as important as low cost over the serviceable life of a valve. Maintaining a Conval valve is far easier and much less costly than replacing a competitor’s valve.
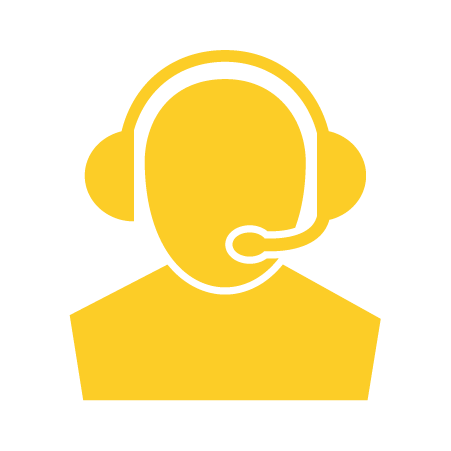
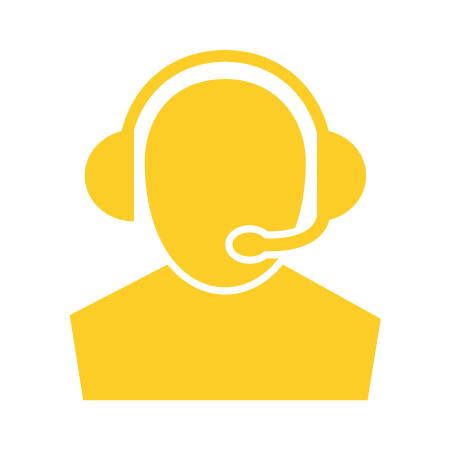
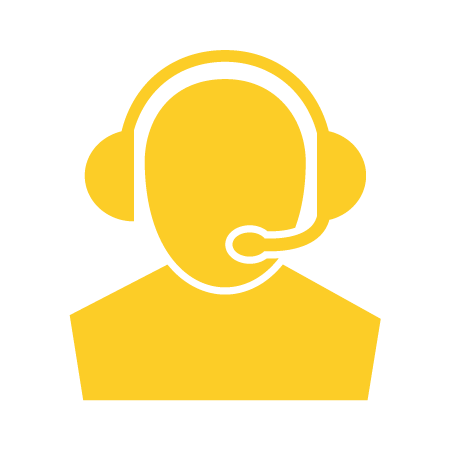
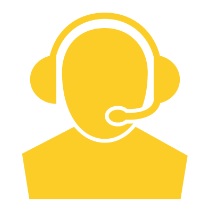
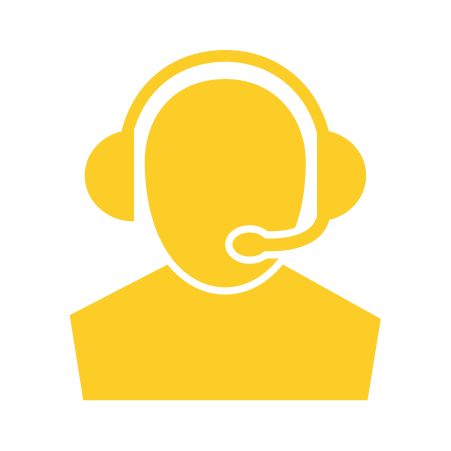