92/38, No.12 Street, Quarter 18, Binh Hung Hoa Ward, Binh Tan District, Ho Chi Minh City, Vietnam.
404 error page Not Found!
We could not find the page you requested or the requested page is not currently available. If this error occurs on a regular basis, please inform us about the problem you are having.
PHUC MINH ENGINEERING CO., LTD is pleased to serve you!
Category
Online support
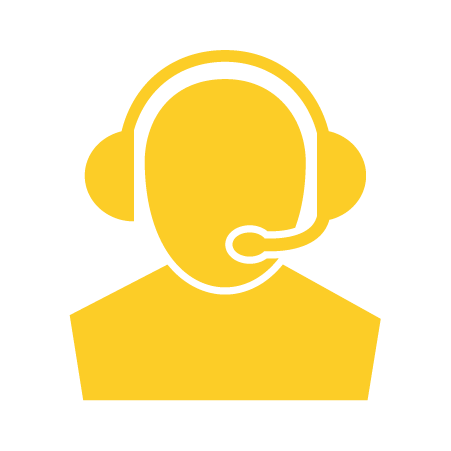
Consulting - Quotation
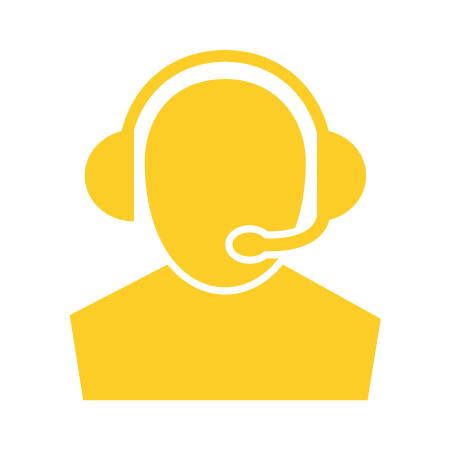
Consulting-Technical
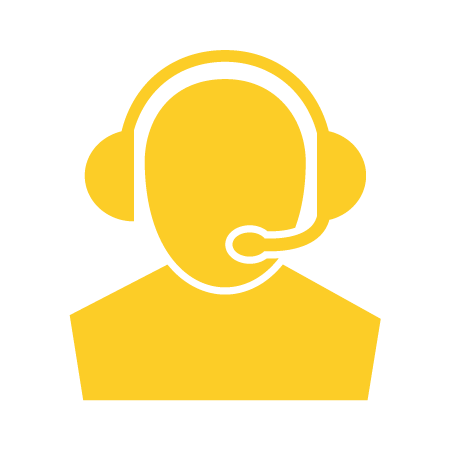
Consulting - Quotation
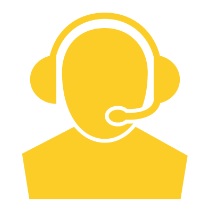
Consulting - Technical
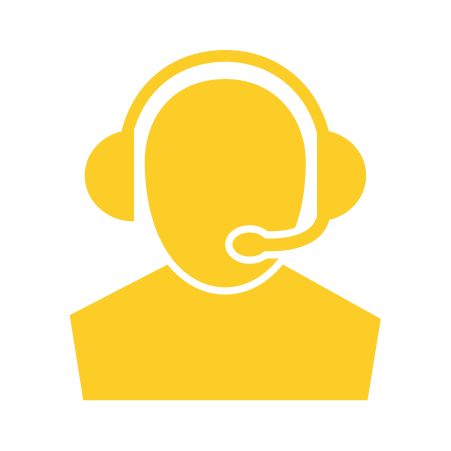
Consulting - Quotation
Featured products